Automatic terminal crimping machine
A terminal crimping machine and terminal crimping technology, applied in the direction of electrical components, circuits, connections, etc., can solve the problems of low efficiency, low efficiency, and impossibility of manual stripping
- Summary
- Abstract
- Description
- Claims
- Application Information
AI Technical Summary
Problems solved by technology
Method used
Image
Examples
Embodiment Construction
[0039] like figure 1 and figure 2 As shown, the fully automatic terminal crimping machine of this embodiment includes a wire feeding mechanism 1 for transmitting the wire harness of the terminal to be crimped;
[0040] The first crimping mechanism 2 divides the first end of the wire harness and performs terminal crimping on the divided wires in sequence;
[0041] The second crimping mechanism 3 divides the second end of the wire harness and performs terminal crimping on the divided wires in sequence;
[0042] The front peeling and shifting mechanism 4 performs peeling operation on the first end of the wire harness, and moves the wire harness to the second pressing mechanism after the first end is crimped;
[0043] The rear peeling and tangent mechanism 5 performs tangent operation on both ends of the wire harness, and performs peeling operation on the second section during the process of moving the wire harness to the second pressing mechanism after the first end is crimped...
PUM
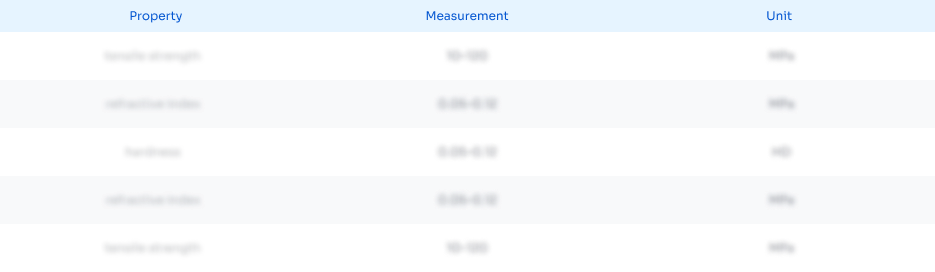
Abstract
Description
Claims
Application Information

- R&D
- Intellectual Property
- Life Sciences
- Materials
- Tech Scout
- Unparalleled Data Quality
- Higher Quality Content
- 60% Fewer Hallucinations
Browse by: Latest US Patents, China's latest patents, Technical Efficacy Thesaurus, Application Domain, Technology Topic, Popular Technical Reports.
© 2025 PatSnap. All rights reserved.Legal|Privacy policy|Modern Slavery Act Transparency Statement|Sitemap|About US| Contact US: help@patsnap.com