Copolymerization-immobilized beta-cyclodextrin porous separation material as well as preparation method and application thereof
A separation material, cyclodextrin technology, applied in chemical instruments and methods, other chemical processes, adsorption water/sewage treatment, etc., can solve the problem of particle surface reduction
- Summary
- Abstract
- Description
- Claims
- Application Information
AI Technical Summary
Problems solved by technology
Method used
Image
Examples
Embodiment 1
[0022] Firstly, 2.27g β-CD was added into 50mL / 50mL anhydrous DMF / anhydrous DMSO mixed solution to fully dissolve β-CD, then 8.96g NaOH was added and stirred vigorously for 1h to mix well. Slowly add 14.4 mL of LC in an ice-water bath at 5°C while stirring 3 h 5 Br, reacted under vigorous stirring for 48 hours, filtered to remove the solid precipitate after the reaction stopped, added 8 to 10 times of water to the filtrate to precipitate the product, extracted with ethyl acetate and then rotary evaporated to obtain vinyl β-CD.
[0023] At room temperature, mix 1g of vinyl β-CD and 2g of styrene evenly, add 0.75g of p-vinylbenzene and 1.01g of Span 80 to form a continuous phase; mix 0.188g of K 2 SO 4 and 0.075gK 2 S 2 o 8 Dissolve in 45g of deionized water to form a dispersed phase. Slowly drop the dispersed phase into the continuous phase under high-speed stirring, and stir evenly after the dropwise addition to form a reverse-phase thick emulsion. Then, the concentrate...
Embodiment 2
[0025] Firstly, add 2.27g β-CD into 40mL / 60mL anhydrous DMF / anhydrous DMSO mixed solution to fully dissolve β-CD, then add 5.04g NaOH and stir vigorously for 1h to mix well. Slowly add 11.4 mL of LC in a water bath at 20°C while stirring 3 h 5 Br, reacted under vigorous stirring for 72 hours, filtered to remove the solid precipitate after the reaction stopped, added 8 to 10 times of water to the filtrate to precipitate the product, extracted with ethyl acetate and rotary evaporated to obtain vinyl β-CD.
[0026] At room temperature, stir and mix 0.6g vinyl β-CD and 2.4g styrene evenly, add 0.375g p-vinylbenzene and 0.505g Span 80 to configure the continuous phase; mix 0.188g K 2 SO 4 and 0.075gK 2 S 2 o 8 Dissolve in 47g of deionized water to form a dispersed phase. Slowly drop the dispersed phase into the continuous phase under high-speed stirring, and stir evenly after the dropwise addition to form a reverse-phase thick emulsion. Then, the concentrated emulsion was pl...
Embodiment 3
[0028] First, add 2.27g β-CD into 40mL / 60mL anhydrous DMF / anhydrous DMSO mixed solution to fully dissolve β-CD, then add 4.04g NaOH and stir vigorously for 1h to mix well. Slowly add 11.4 mL of LC in a water bath at 20°C while stirring 3 h 5 Br, reacted under vigorous stirring for 72 hours, filtered to remove the solid precipitate after the reaction stopped, added 8 to 10 times of water to the filtrate to precipitate the product, extracted with ethyl acetate and rotary evaporated to obtain vinyl β-CD.
[0029] At room temperature, stir and mix 1g vinyl β-CD and 2g styrene evenly, add 0.375g p-vinylbenzene, 1.405g Span 20 to configure the continuous phase; mix 0.188g K 2 SO 4 and 0.075gK 2 S 2 o 8 Dissolve in 45g of deionized water to form a dispersed phase. Slowly drop the dispersed phase into the continuous phase under high-speed stirring, and stir evenly after the dropwise addition to form a reverse-phase thick emulsion. Then, the concentrated emulsion was placed in a...
PUM
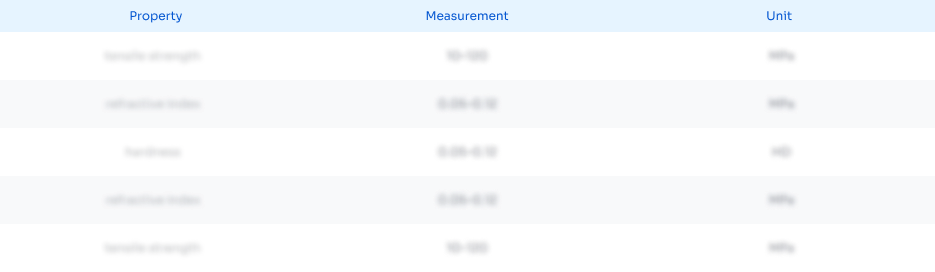
Abstract
Description
Claims
Application Information

- R&D
- Intellectual Property
- Life Sciences
- Materials
- Tech Scout
- Unparalleled Data Quality
- Higher Quality Content
- 60% Fewer Hallucinations
Browse by: Latest US Patents, China's latest patents, Technical Efficacy Thesaurus, Application Domain, Technology Topic, Popular Technical Reports.
© 2025 PatSnap. All rights reserved.Legal|Privacy policy|Modern Slavery Act Transparency Statement|Sitemap|About US| Contact US: help@patsnap.com