Formula and preparation method of ultralow temperature glaze
A technology of ultra-low temperature and glaze, which is applied in the formulation and preparation of ultra-low temperature glaze, which can solve the problems of uneven color, poor color rendering effect, and prone to glaze bubbles, etc., achieve clear color, reduce firing temperature, and combine good effect
- Summary
- Abstract
- Description
- Claims
- Application Information
AI Technical Summary
Problems solved by technology
Method used
Image
Examples
Embodiment 1
[0018] The preparation method of ultra-low temperature glaze comprises the following steps:
[0019] (1) Preparation of raw materials: Calcining borax, talc powder and star kaolin at high temperature at 400°C, 1400°C and 1400°C respectively to obtain raw materials;
[0020] (2) Mixing materials: 32kg of calcined borax, 23kg of potassium feldspar, 8kg of calcined talcum powder, 6kg of quartz, 8kg of Xinhui powder, 5kg of calcined Xingzi kaolin in parts by weight , 4kg of limestone, 8kg of Suzhou soil, 0.5kg of titanium dioxide, 6kg of levodolite and 15kg of zinc oxide were mixed and stirred evenly to obtain a premix.
[0021] (3) Ball milling: The premix prepared in step (2) is wet ball milled until the particle size of the premix passes through a 325-mesh sieve, and the sieve residue is 4% and the water content is 42%;
[0022] (4) Preparation of ultra-low temperature glaze: the material after ball milling in step (3) is glazed, dried, and calcined to obtain an ultra-low temp...
Embodiment 2
[0025] Embodiment 2: the preparation method of ultra-low temperature glaze, comprises the following steps:
[0026] (1) Preparation of raw materials: Calcining borax, talc powder and star kaolin at high temperature at 400°C, 1400°C and 1400°C respectively to obtain raw materials;
[0027] (2) Mixing materials: 36kg of calcined borax, 21kg of potassium feldspar, 15kg of calcined talcum powder, 8kg of quartz, 9kg of Xinhui powder, and 8kg of calcined Xingzi kaolin in parts by weight , 7kg of limestone, 3kg of Suzhou soil, 1kg of titanium dioxide, 2kg of levodolite and 5kg of zinc oxide were mixed and stirred evenly to obtain a premix.
[0028] (3) Ball milling: the premix prepared in step (2) is wet ball milled until the particle size of the premix passes through a 325-mesh sieve, and the sieve residue is 6% and the water content is 42%;
[0029] (4) Preparation of ultra-low temperature glaze: the material after ball milling in step (3) is glazed, dried, and calcined to obtain ...
Embodiment 3
[0033] The preparation method of ultra-low temperature glaze comprises the following steps:
[0034] (1) Preparation of raw materials: Calcining borax, talc powder and star kaolin at high temperature at 400°C, 1400°C and 1400°C respectively to obtain raw materials;
[0035] (2) Mixing materials: 34kg of calcined borax, 22kg of potassium feldspar, 12kg of calcined talcum powder, 7kg of quartz, 8kg of Xinhui powder, and 7kg of calcined Xingzi kaolin in parts by weight , 6kg of limestone, 5kg of Suzhou soil, 0.8kg of titanium dioxide, 4kg of levodolite and 10kg of zinc oxide were mixed and stirred evenly to obtain a premix.
[0036] (3) Ball milling: The premix prepared in step (2) is wet ball milled until the particle size of the premix passes through a 325-mesh sieve, and the sieve residue is 5% and the water content is 42%;
[0037] (4) Preparation of ultra-low temperature glaze: the material after ball milling in step (3) is glazed, dried, and calcined to obtain an ultra-low...
PUM
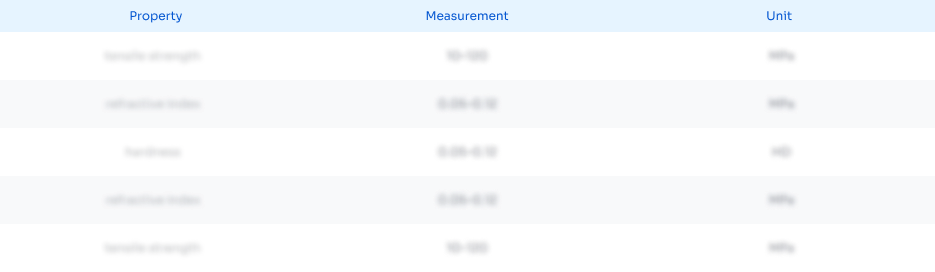
Abstract
Description
Claims
Application Information

- Generate Ideas
- Intellectual Property
- Life Sciences
- Materials
- Tech Scout
- Unparalleled Data Quality
- Higher Quality Content
- 60% Fewer Hallucinations
Browse by: Latest US Patents, China's latest patents, Technical Efficacy Thesaurus, Application Domain, Technology Topic, Popular Technical Reports.
© 2025 PatSnap. All rights reserved.Legal|Privacy policy|Modern Slavery Act Transparency Statement|Sitemap|About US| Contact US: help@patsnap.com