Integrated machining method of planet carrier of robot RV reducer
A processing method and reducer technology, which is applied in the field of integrated processing of robot RV reducer planetary frame, can solve the problem that the installation accuracy of tapered roller bearings cannot be guaranteed, the crankshaft position and coaxiality cannot be guaranteed, and the robot RV reducer Low precision and other problems, to achieve the effect of reducing the machining allowance, increasing the processing size, and increasing the output torque
- Summary
- Abstract
- Description
- Claims
- Application Information
AI Technical Summary
Problems solved by technology
Method used
Image
Examples
Embodiment Construction
[0023] In order to make the object, technical solution and advantages of the present invention clearer, the present invention will be further described in detail below in conjunction with the accompanying drawings and embodiments. It should be understood that the specific embodiments described here are only used to explain the present invention, not to limit the present invention.
[0024] Such as figure 1 with figure 2 Commonly shown, the machining method for the integration of the planet carrier of the robot RV reducer includes the following steps:
[0025] (1) Forging the first casing 1 and the second casing 2 respectively;
[0026] (2) Extruding the first shell 1 and the second shell 2 respectively;
[0027] (3) Perform quenching and tempering treatment on both the hot-extruded first shell 1 and the second shell 2;
[0028] (4) Perform tempering treatment on both the quenched and tempered first shell 1 and the second shell 2;
[0029] (5) Finishing the end faces of t...
PUM
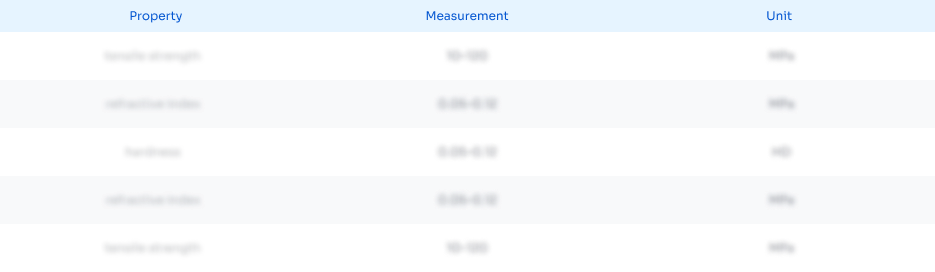
Abstract
Description
Claims
Application Information

- R&D
- Intellectual Property
- Life Sciences
- Materials
- Tech Scout
- Unparalleled Data Quality
- Higher Quality Content
- 60% Fewer Hallucinations
Browse by: Latest US Patents, China's latest patents, Technical Efficacy Thesaurus, Application Domain, Technology Topic, Popular Technical Reports.
© 2025 PatSnap. All rights reserved.Legal|Privacy policy|Modern Slavery Act Transparency Statement|Sitemap|About US| Contact US: help@patsnap.com