Double-faced flat-bulging process of pure aluminum panel
A plate, double-sided technology, used in the field of inflation technology, can solve the problems of easy damage to the flat surface and inability to meet the requirements of use, and achieve the effects of easy superimposed heat transfer, good welding performance, and widening the scope of use.
- Summary
- Abstract
- Description
- Claims
- Application Information
AI Technical Summary
Problems solved by technology
Method used
Examples
Embodiment 1
[0024] The surface of the selected aluminum plate with a thickness of 1.5 mm, 5.0 mm, and 5.0 mm is roughened with a wire roller brush, and the aluminum powder attached to the surface is blown off with 0.3-0.8 MPa dry air. After the temperature of the aluminum plate dropped to room temperature, different graphite circuit diagrams were printed on the two polished surfaces of the aluminum plate with a thickness of 1.5 mm. Two aluminum plates with a thickness of 5.0 mm sandwich a 1.5 mm thick aluminum plate with graphite line patterns on both sides, and the three sides are aligned and riveted along the edges. After the riveted aluminum plate is heated by the heating furnace, it is sent to the hot rolling mill for rolling. According to the requirements of different specifications, the aluminum plate of the required length can be obtained. Anneal the aluminum plate with qualified length in the annealing furnace and cool it to room temperature; drill a process hole on the graphite l...
PUM
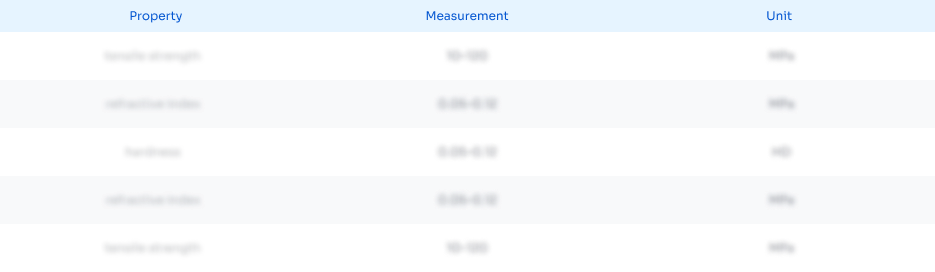
Abstract
Description
Claims
Application Information

- R&D Engineer
- R&D Manager
- IP Professional
- Industry Leading Data Capabilities
- Powerful AI technology
- Patent DNA Extraction
Browse by: Latest US Patents, China's latest patents, Technical Efficacy Thesaurus, Application Domain, Technology Topic, Popular Technical Reports.
© 2024 PatSnap. All rights reserved.Legal|Privacy policy|Modern Slavery Act Transparency Statement|Sitemap|About US| Contact US: help@patsnap.com