Aero-engine blade damage repair method
An aero-engine and repair method technology, applied in welding equipment, metal processing equipment, plasma welding equipment, etc., can solve problems such as large welding spatter, and achieve the effects of good forming accuracy, improved welding seam forming, and high welding accuracy
- Summary
- Abstract
- Description
- Claims
- Application Information
AI Technical Summary
Problems solved by technology
Method used
Image
Examples
Embodiment Construction
[0025] The present invention will be further described below in conjunction with the embodiments and accompanying drawings, but the specific embodiments do not limit the protection scope of the claims of the application.
[0026] The repair method (abbreviation repair method) of the aeroengine blade (abbreviation blade) damage designed by the present invention, see Figure 1-7 ) adopt the following equipment combination system and repair process:
[0027] The equipment combination system includes an ABB robot 1 and its accompanying program control system 2, welding power supply 3, plasma generator 4, wire feeder 5 and plasma welding torch 6; the robot 1 is connected with the program control system 2 through a control cable; the robot The program control system 2 and the welding power supply 3 adopt bus communication; the plasma generator 4 is connected with the welding power supply 3 through a control cable; the wire feeder 5 is installed on the robot 1 and connected with the ...
PUM
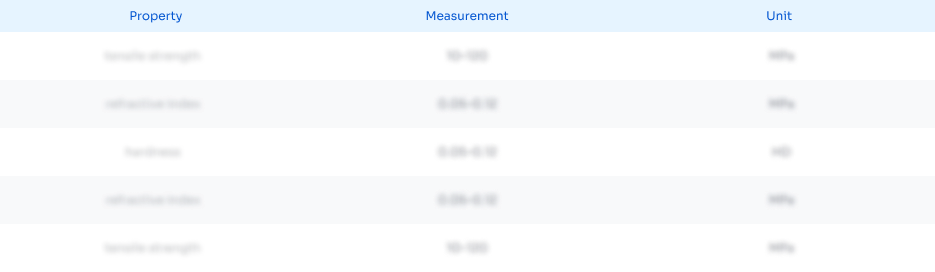
Abstract
Description
Claims
Application Information

- R&D Engineer
- R&D Manager
- IP Professional
- Industry Leading Data Capabilities
- Powerful AI technology
- Patent DNA Extraction
Browse by: Latest US Patents, China's latest patents, Technical Efficacy Thesaurus, Application Domain, Technology Topic, Popular Technical Reports.
© 2024 PatSnap. All rights reserved.Legal|Privacy policy|Modern Slavery Act Transparency Statement|Sitemap|About US| Contact US: help@patsnap.com