Wastewater treatment method for wet regeneration of mixed casting waste sand
A technology for waste foundry sand and wet regeneration, applied in water/sewage multi-stage treatment, water/sludge/sewage treatment, chemical instruments and methods, etc. The problem of high mud moisture content can reduce the moisture content, reduce the floor space and increase the settlement area.
- Summary
- Abstract
- Description
- Claims
- Application Information
AI Technical Summary
Problems solved by technology
Method used
Image
Examples
Embodiment 1
[0026] The wastewater treatment method for wet regeneration of mixed casting waste sand comprises the following steps:
[0027] (1) Demulsification: By adding 0.01% AR demulsifier to the wastewater, the emulsified liquid structure is destroyed, so as to separate the solid and liquid phases in the emulsion;
[0028] (2) Primary flocculation: pump the wastewater into the first-stage spiral flocculation tank, add polyaluminium chloride with a weight concentration of 10%, and add 1 / 800 of the wastewater weight, and flocculate for 20 seconds.
[0029] (3) Secondary flocculation: transfer the material in the primary spiral flocculation tank to the secondary spiral flocculation tank, add polyacrylamide (PAM) solution with a weight concentration of 0.1%, the amount added is 1 / 800 of the weight of the wastewater, and flocculate 80 seconds, then transfer the material in the secondary spiral flocculation tank to the inclined plate thickening box, and let it settle for 30 minutes;
[003...
Embodiment 2
[0032] The wastewater treatment method for wet regeneration of mixed casting waste sand comprises the following steps:
[0033] (1) Demulsification: By adding 0.03% AR demulsifier to the wastewater, the emulsified liquid structure is destroyed, so as to separate the solid and liquid phases in the emulsion;
[0034] (2) Primary flocculation: pump the wastewater into the first-stage spiral flocculation tank, add polyaluminum sulfate solution with a weight concentration of 10%, the amount added is 1 / 1000 of the wastewater weight, and flocculate for 30 seconds.
[0035] (3) Secondary flocculation: Transfer the material in the primary spiral flocculation tank into the secondary spiral flocculation tank, add PAM solution with a weight concentration of 0.2%, and the amount added is 1 / 1000 of the wastewater weight, flocculate for 70 seconds, and then put The material in the secondary spiral flocculation tank is transferred to the inclined plate thickening box, and left to settle for 4...
Embodiment 3
[0038] The wastewater treatment method for wet regeneration of mixed casting waste sand comprises the following steps:
[0039] (1) Demulsification: By adding 0.05% AR demulsifier to the waste water, the emulsified liquid structure is destroyed, so as to separate the solid and liquid phases in the emulsion;
[0040] (2) Primary flocculation: pump the wastewater into the first-stage spiral flocculation tank, add polyferric sulfate solution with a weight concentration of 10%, the amount added is 1 / 1200 of the wastewater weight, and flocculate for 50 seconds.
[0041] (3) Secondary flocculation: transfer the material in the primary spiral flocculation tank to the secondary spiral flocculation tank, and add polydimethyldiallylammonium chloride (PDMDAAC) solution with a weight concentration of 0.3%, and the addition amount is 1 / 1100 of the waste water weight, flocculate for 60 seconds, then transfer the material in the secondary spiral flocculation tank to the inclined plate thicke...
PUM
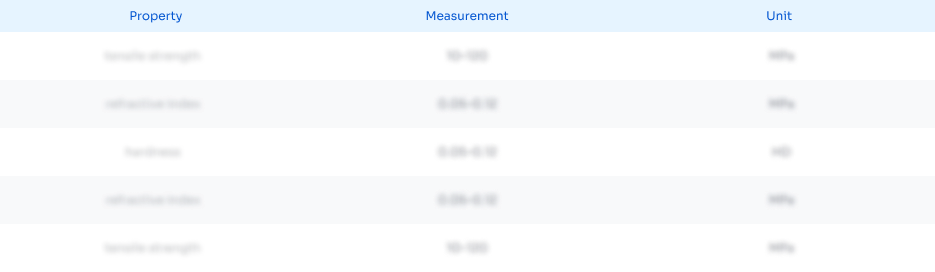
Abstract
Description
Claims
Application Information

- R&D
- Intellectual Property
- Life Sciences
- Materials
- Tech Scout
- Unparalleled Data Quality
- Higher Quality Content
- 60% Fewer Hallucinations
Browse by: Latest US Patents, China's latest patents, Technical Efficacy Thesaurus, Application Domain, Technology Topic, Popular Technical Reports.
© 2025 PatSnap. All rights reserved.Legal|Privacy policy|Modern Slavery Act Transparency Statement|Sitemap|About US| Contact US: help@patsnap.com