Rail vibration absorber
A vibration absorber and track technology, applied in the field of vibration reduction devices, can solve the problems of unstable performance, limited vibration reduction and noise reduction effect, scratches and damages from external objects, etc., and achieves high efficiency and stability in vibration reduction performance, significant vibration reduction effect, and prolonged The effect of the service life
- Summary
- Abstract
- Description
- Claims
- Application Information
AI Technical Summary
Problems solved by technology
Method used
Image
Examples
Embodiment 1
[0057] like figure 1 The rail shock absorber of the present invention as shown includes an elastic element 4 and a mass block 3, and also includes a coupling frame 2. The surface shape of the coupling frame 2 and the rail 1 flange and the rail waist coupling part is the same as that of the corresponding surface of the rail. The coupling frame 2 includes a vibration-absorbing cavity 100 , the mass block 3 is arranged in the vibration-absorbing cavity 100 of the coupling frame 2 , and an elastic element 4 is arranged between the mass block 3 and the wall of the vibration-absorbing cavity 100 . Specifically, the elastic element 4 is vertically arranged between the mass block 3 and the wall of the vibration-absorbing cavity 100 along the rail, the coupling frame 2 is made of aluminum alloy material, and the elastic element 4 is made of rubber material, because the rubber material has good damping It is a commonly used elastic solid damping material, so the elastic element 4 is als...
Embodiment 2
[0073] like figure 2The rail vibration absorber of the present invention shown differs from Embodiment 1 in that the elastic element 4 is arranged between the mass block 3 and the vertical cavity wall surface of the vibration-absorbing cavity 100 corresponding to the rail 1, and the coupling frame 2 is made of glass fiber reinforced plastic material, elastic The element 4 is made of high-damping elastic polyurethane material, and the mass block 3 is made of steel material, wherein the elastic element 4 is fixedly connected with the mass block 3 and the wall of the vibration-absorbing cavity 100 through chemical bonding process. In order to increase the reliability of the connection between the elastic element, the coupling frame and the mass block, a connection strengthening structure is respectively provided on the mating surface of the coupling frame and the elastic element and the mating surface of the mass block and the elastic element. The connection strengthening structu...
Embodiment 3
[0078] Such as image 3 The difference between the rail vibration absorber of the present invention shown in Embodiment 1 is that the coupling frame 2 is made of steel, and the elastic element 4 is arranged between the mass block 3 and the wall surface of the vibration-absorbing cavity 100 corresponding to the transverse direction of the rail 1. The elastic element 4 A metal spring is adopted, specifically a helical steel spring in this example, and the two ends of the helical steel spring are respectively welded and fixed on the connection frame 2 and the mass block 3 . In addition, in order to ensure that the elastic element 4 always forms an effective support for the mass block 3 during use, the elastic element 4 is pre-compressed when it is assembled with the mass block 3 and the coupling frame 2, and is in a pre-compressed state, and the elastic element 4 The pre-compression displacement is greater than the vibration amplitude of the mass block 3 relative to the wall of t...
PUM
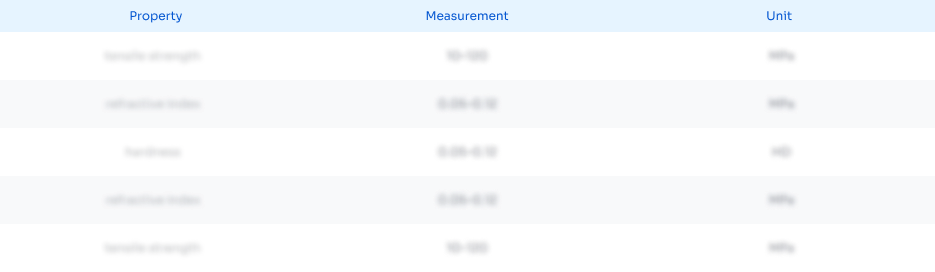
Abstract
Description
Claims
Application Information

- R&D
- Intellectual Property
- Life Sciences
- Materials
- Tech Scout
- Unparalleled Data Quality
- Higher Quality Content
- 60% Fewer Hallucinations
Browse by: Latest US Patents, China's latest patents, Technical Efficacy Thesaurus, Application Domain, Technology Topic, Popular Technical Reports.
© 2025 PatSnap. All rights reserved.Legal|Privacy policy|Modern Slavery Act Transparency Statement|Sitemap|About US| Contact US: help@patsnap.com