A corrugated foil mold and its manufacturing process
A corrugated foil and mold technology, applied in the field of corrugated foil mold and its manufacturing process, can solve the high requirements of bearing machining accuracy and assembly precision, the rotor system is difficult to meet the reliability and stability, and the corrugated foil manufacturing process is complex and other problems, to achieve the effect of convenient and fast manufacturing process, high structural size and smooth surface
- Summary
- Abstract
- Description
- Claims
- Application Information
AI Technical Summary
Problems solved by technology
Method used
Image
Examples
Embodiment Construction
[0030] The technical solution of the present invention will be described in detail below in conjunction with the accompanying drawings.
[0031] Please refer to figure 1 and combine Figure 2 to Figure 5 As shown, the corrugated foil mold of the present invention includes four parts: a mold chassis 1 , a positioning block 2 , a spacer 3 and a pressing block 4 . A concave mold corresponding to the corrugated foil sheet 5 is processed on the mold chassis 1. The concave mold here refers to the first annular gap 8 and the groove 9 on the mold chassis 1 described below. Along the two mutually perpendicular gaps 6 in the circumferential direction and the vertical direction, the two M2 socket head cap screws 7 in the screw holes of the positioning block 2 fix the corrugated foil 5 by pressing the gasket 3 in the rectangular groove 12 .
[0032] The first annular gap 8 and the groove 9 on the mold chassis 1 correspond to the distribution of the second annular gap 10 and the foil arc...
PUM
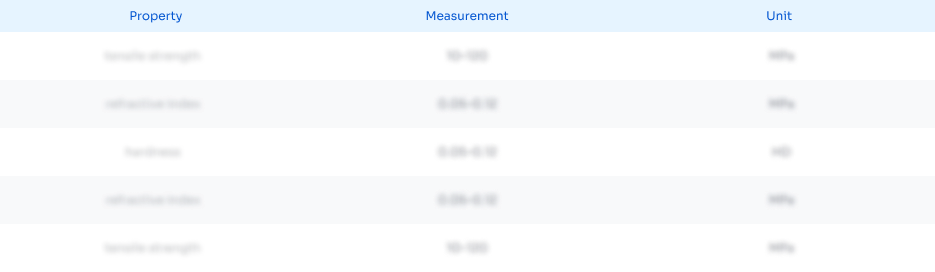
Abstract
Description
Claims
Application Information

- Generate Ideas
- Intellectual Property
- Life Sciences
- Materials
- Tech Scout
- Unparalleled Data Quality
- Higher Quality Content
- 60% Fewer Hallucinations
Browse by: Latest US Patents, China's latest patents, Technical Efficacy Thesaurus, Application Domain, Technology Topic, Popular Technical Reports.
© 2025 PatSnap. All rights reserved.Legal|Privacy policy|Modern Slavery Act Transparency Statement|Sitemap|About US| Contact US: help@patsnap.com