Fire-proof electric wire and manufacturing method thereof
A wire and fire-resistant technology, used in cable/conductor manufacturing, circuits, power cables, etc., can solve problems such as low temperature resistance, spontaneous combustion of wires, and easy aging.
- Summary
- Abstract
- Description
- Claims
- Application Information
AI Technical Summary
Problems solved by technology
Method used
Image
Examples
Embodiment Construction
[0015] Below in conjunction with accompanying drawing, a kind of fireproof refractory electric wire of the present invention and manufacturing method are described as follows:
[0016] Such as figure 1 As shown, the fire-proof and refractory electric wire of the present invention comprises a copper conductor 1, and the outside of the copper conductor 1 is coated with a temperature-insulating fire-proof layer 2, a fire-resistant insulating layer 3, and a waterproof insulating layer 4; One of ceramic fiber yarn and dust-free asbestos thread; the fire-resistant insulating layer 3 is made of alkali-free glass fiber yarn; the waterproof insulating layer 4 is made of one of rubber mixture and polyvinyl chloride mixture. made.
[0017] The manufacturing method of the fireproof and refractory electric wire of the present invention comprises the following steps:
[0018] A. First use the electronic rewinding machine to rewind the ceramic fiber wire to the special wire roller, and ins...
PUM
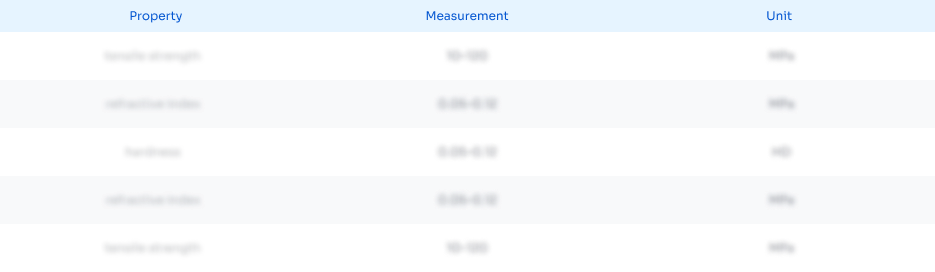
Abstract
Description
Claims
Application Information

- R&D
- Intellectual Property
- Life Sciences
- Materials
- Tech Scout
- Unparalleled Data Quality
- Higher Quality Content
- 60% Fewer Hallucinations
Browse by: Latest US Patents, China's latest patents, Technical Efficacy Thesaurus, Application Domain, Technology Topic, Popular Technical Reports.
© 2025 PatSnap. All rights reserved.Legal|Privacy policy|Modern Slavery Act Transparency Statement|Sitemap|About US| Contact US: help@patsnap.com