Method for prolonging service life of top-bottom composite blowing converter bottom
A converter bottom and service life technology, which is applied to the bottom compound blowing converter bottom service life, prolongs the converter bottom service life, improves the roof area, and can solve the problem of affecting normal steelmaking production, shortening the converter bottom service life, and breathable bricks Erosion speed is fast and other problems, to achieve the effect of reducing smelting cycle, improving service life and improving production efficiency
- Summary
- Abstract
- Description
- Claims
- Application Information
AI Technical Summary
Problems solved by technology
Method used
Examples
Embodiment 1
[0029] The method for improving the service life of top and bottom compound blowing converter bottoms is characterized in that the steps are as follows:
[0030] (1) During the normal top-bottom compound blowing process, in addition to visual observation, measure the furnace bottom with a furnace bottom measuring rod every 8 hours, and determine the corrosion of the furnace bottom by comparing it with the original furnace bottom. Focus on the parts with severe corrosion, and draw the corrosion trend chart of the bottom of the furnace according to the data of each measurement; when the air permeability of the bottom of the furnace is 20Nm 3 When the conventional magnesia-carbon refractory breathable brick with a pressure of 1.0Mpa melts and loses 100mm per hour, after the steel is tapped and the slag is poured out, add a solidification temperature of 800 ℃ of the following mass ratio of filling materials: MgO: 75%, C: 14%, CaO: 1%, SiO 2 : 2%, Fe 2 o 3 : 0.5%, phenolic res...
Embodiment 2
[0034] The method for improving the service life of top and bottom compound blowing converter bottoms is characterized in that the steps are as follows:
[0035] (1) During the normal top-bottom compound blowing process, in addition to visual observation, measure the furnace bottom with a furnace bottom measuring rod every 10 hours, and determine the corrosion of the furnace bottom by comparing it with the original furnace bottom. Focus on the parts with severe corrosion, and draw the corrosion trend chart of the bottom of the furnace according to the data of each measurement; when the gas flow of the bottom of the furnace is 30Nm 3 When the conventional magnesia-carbon refractory ventilated brick with a pressure of 0.2 Mpa has a melting loss of 150mm per hour, after the steel is tapped and the slag is poured out, add a solidification temperature of 1000 ℃ of the following mass ratio of filling materials: MgO: 85%, C: 7%, CaO: 3%, SiO 2 : 1%, Fe 2 o 3 : 1.5%, asphalt: 2.5...
Embodiment 3
[0039] The method for improving the service life of top and bottom compound blowing converter bottoms is characterized in that the steps are as follows:
[0040] (1) During the normal top-bottom compound blowing process, in addition to visual observation, the furnace bottom is measured every 9 hours with a furnace bottom measuring rod, and the corrosion of the furnace bottom is determined by comparing with the original furnace bottom. Focus on the parts with severe corrosion, and draw the corrosion trend chart of the bottom of the furnace according to the data of each measurement; when the gas flow of the bottom of the furnace is 25Nm 3 / h, pressure of 0.6Mpa conventional magnesia-carbon refractory breathable brick melting loss of 130mm, after the steel is tapped and the slag is poured out, according to the amount of 100mm in thickness each time, add solidification temperature to the furnace 900 ℃ of the following mass ratio of filling materials: MgO: 80%, C: 10%, CaO: 2%, SiO...
PUM
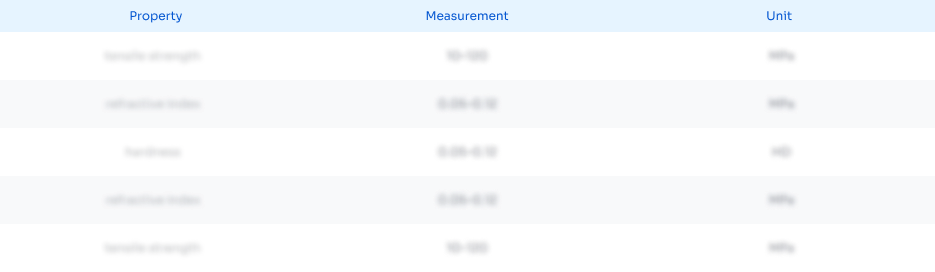
Abstract
Description
Claims
Application Information

- R&D
- Intellectual Property
- Life Sciences
- Materials
- Tech Scout
- Unparalleled Data Quality
- Higher Quality Content
- 60% Fewer Hallucinations
Browse by: Latest US Patents, China's latest patents, Technical Efficacy Thesaurus, Application Domain, Technology Topic, Popular Technical Reports.
© 2025 PatSnap. All rights reserved.Legal|Privacy policy|Modern Slavery Act Transparency Statement|Sitemap|About US| Contact US: help@patsnap.com