Glyphographic binding technology
A technology, electric engraving technology, applied in printing, printing plate preparation, etc., can solve the problems of complex laser plate processing, shorten the printing time of customers, and long cycle, and achieve the effect of reducing plate-making costs, facilitating promotion, and easy operation
- Summary
- Abstract
- Description
- Claims
- Application Information
AI Technical Summary
Problems solved by technology
Method used
Image
Examples
Embodiment 1
[0014] An electric engraving and binding process. This process uses a combined engraving method for two engravings. First, a 0.25mm wide line is carved around the selected pattern, and then the line and the selected pattern are expanded and contracted by 0.1mm. Leave a 0.15mm engraving amount, first use the rough carving process to carve the selected pattern, and then use the fine carving process to sculpt the surrounding lines, so that the two dots are exactly connected, and the fine lines carved afterwards are just the jagged edges of the rough carving. Pressed together. I can't see any aliasing. Such as figure 1 Shown.
Embodiment 2
[0016] An electric engraving and edge binding process. This process uses a combined engraving method for two engravings, first engraving a 0.2mm wide line around the selected pattern, and then expanding and contracting the line and the selected pattern by 0.05mm. Leave a 0.1mm engraving amount, first use the rough carving process to carve the selected pattern, and then use the fine carving process to sculpt the surrounding lines, so that the two dots are just connected, and the fine line after the carving is just the jagged edge of the rough carving. Pressed together.
Embodiment 3
[0018] An electric engraving and binding process. This process uses a combined engraving method for two engravings, first engraving a 0.3mm wide line around the selected pattern, and then expanding and contracting the line and the selected pattern by 0.15mm. Leave a 0.2mm engraving amount, first use the rough carving process to carve the selected pattern, and then use the fine carving process to sculpt the surrounding lines so that the two dots are exactly connected, and the fine lines carved afterwards just match the jagged edges of the rough carving. Pressed together.
PUM
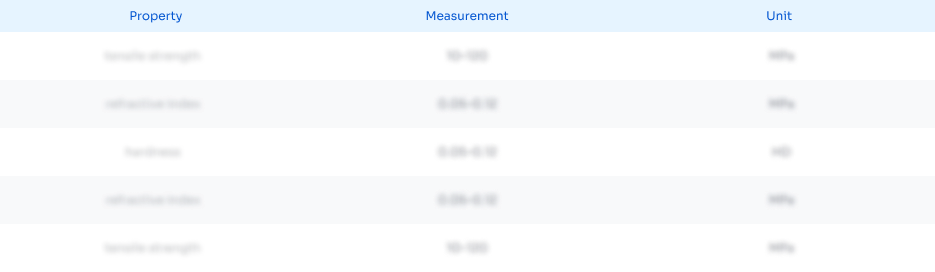
Abstract
Description
Claims
Application Information

- R&D
- Intellectual Property
- Life Sciences
- Materials
- Tech Scout
- Unparalleled Data Quality
- Higher Quality Content
- 60% Fewer Hallucinations
Browse by: Latest US Patents, China's latest patents, Technical Efficacy Thesaurus, Application Domain, Technology Topic, Popular Technical Reports.
© 2025 PatSnap. All rights reserved.Legal|Privacy policy|Modern Slavery Act Transparency Statement|Sitemap|About US| Contact US: help@patsnap.com