Novel glass mat-reinforced thermoplastic (GMT) board and production process thereof
A new type of sheet material, applied in the direction of layered products, synthetic resin layered products, glass/slag layered products, etc., can solve problems such as environmental pollution, glass fiber has no affinity, and resin matrix and glass fiber cross-section are difficult to combine , to achieve huge environmental benefits, reduce vehicle weight, and simple structure
- Summary
- Abstract
- Description
- Claims
- Application Information
AI Technical Summary
Problems solved by technology
Method used
Examples
Embodiment Construction
[0016] In order to make the technical means, creative features, objectives and effects achieved by the present invention easy to understand, the present invention is further elaborated.
[0017] A new type of GMT board and its production process, characterized in that it comprises polypropylene fiber, alkali-free coarse glass fiber and alkali-free fine glass fiber in a ratio of 5:4:1, and the specific process steps include:
[0018] Step 1: Preliminary mixing of polypropylene fiber, alkali-free coarse glass fiber and fine glass fiber at a room temperature of 15-25°C and a humidity of 55%-65%;
[0019] Step 2: Under the environment of room temperature 15-25 ℃ and humidity 55%-65%, use the height of the mixing chamber to make the polypropylene fiber, alkali-free coarse glass fiber and alkali-free fine glass fiber roughly mixed in the form of free fall;
[0020] Step 3: Under the environment of room temperature 15-25 ℃ and humidity 55%-65%, use a fan to blow air into the box, so ...
PUM
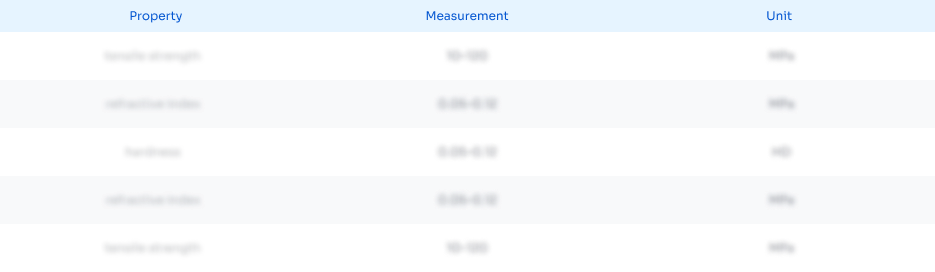
Abstract
Description
Claims
Application Information

- Generate Ideas
- Intellectual Property
- Life Sciences
- Materials
- Tech Scout
- Unparalleled Data Quality
- Higher Quality Content
- 60% Fewer Hallucinations
Browse by: Latest US Patents, China's latest patents, Technical Efficacy Thesaurus, Application Domain, Technology Topic, Popular Technical Reports.
© 2025 PatSnap. All rights reserved.Legal|Privacy policy|Modern Slavery Act Transparency Statement|Sitemap|About US| Contact US: help@patsnap.com