Production technology of reconstituted cut stems
A production process and technology for cut stems, which are applied in the field of the production process for the regeneration of cut stems, can solve the problems of large environmental pollution of the discharge liquid, high processing intensity, and large damage to the cut stems.
- Summary
- Abstract
- Description
- Claims
- Application Information
AI Technical Summary
Problems solved by technology
Method used
Image
Examples
Embodiment 1
[0048] A production process for reconstituted shredded stems, comprising the following steps:
[0049] (1) Mechanically crush the tobacco stems to a length of 20mm, weigh 200kg of crushed tobacco stems, 200kg of tobacco dust and 1800kg of tap water, mix well and heat until the temperature reaches 50°C, and stir for 2.0 hours with a screw. Then use a continuous low-speed extrusion filter to continuously extrude to obtain the extract of tobacco stems and tobacco dust, and the water content of the extruded filter residue is 52%.
[0050] (2) Measure 1000 kg of the extract obtained in step (1), add 5 kg of diatomite and stir evenly, press filter with a cardboard frame fine filter under a pressure of 0.30 Mpa, and use cardboard with a thickness of 4.5 mm and a filter aperture of 2.0 μm Activated carbon filter cardboard, after filtration to obtain a clear filtrate.
[0051] (3) Concentrate the clarified liquid obtained in step (2) under reduced pressure at 65.0°C. The density of th...
Embodiment 2
[0059] A production process for reconstituted shredded stems, comprising the following steps:
[0060] (1) Mechanically crush the tobacco stems to a length of 25.0mm, weigh 200kg of crushed tobacco stems, 200kg of tobacco dust and 1800kg of tap water, heat to a temperature of 60.0°C, and stir for 1.8 hours with a screw. Then use a continuous low-speed extrusion filter to continuously extrude to obtain the extract of tobacco stems and tobacco dust, and the water content of the extruded filter residue is 54%.
[0061] (2) Measure 1000 kg of the extract obtained in step (1), add 5 kg of diatomite and stir evenly, press filter with a cardboard frame fine filter under a pressure of 0.30 Mpa, and use cardboard with a thickness of 4.5 mm and a filter aperture of 2.0 μm Activated carbon filter cardboard, after filtration to obtain a clear filtrate.
[0062] (3) Concentrate the clarified liquid obtained in step (2) under reduced pressure at 68.0°C. The density of the concentrated extr...
Embodiment 3
[0070] A production process for reconstituted shredded stems, comprising the following steps:
[0071] (1) Mechanically crush the tobacco stems to a length of 20.0mm, weigh 200kg of crushed tobacco stems, 200kg of tobacco dust and 1800kg of tap water, heat to a temperature of 55.0°C, and stir for 1.5 hours with a screw. Then, it is continuously extruded by a continuous low-speed extruding filter to obtain an extract of tobacco stems and tobacco dust, and the water content of the extruded filter residue is 51%.
[0072] (2) Measure 1000 kg of the extract obtained in step (1), add 5 kg of diatomite and stir evenly, press filter with a cardboard frame fine filter under a pressure of 0.30 Mpa, and use cardboard with a thickness of 4.5 mm and a filter aperture of 2.0 μm Activated carbon filter cardboard, after filtration to obtain a clear filtrate.
[0073] (3) Concentrate the clarified liquid obtained in step (2) under reduced pressure at 70.0°C. The density of the concentrated e...
PUM
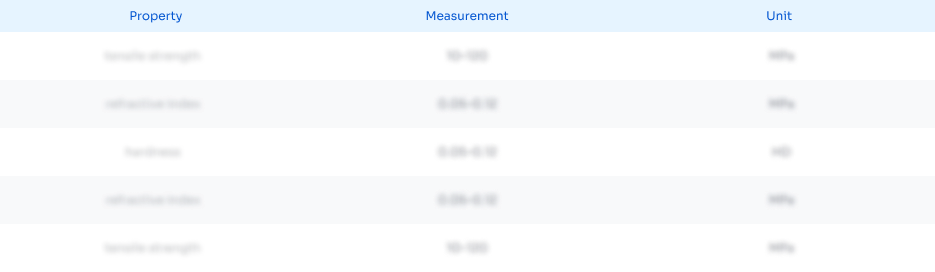
Abstract
Description
Claims
Application Information

- R&D Engineer
- R&D Manager
- IP Professional
- Industry Leading Data Capabilities
- Powerful AI technology
- Patent DNA Extraction
Browse by: Latest US Patents, China's latest patents, Technical Efficacy Thesaurus, Application Domain, Technology Topic, Popular Technical Reports.
© 2024 PatSnap. All rights reserved.Legal|Privacy policy|Modern Slavery Act Transparency Statement|Sitemap|About US| Contact US: help@patsnap.com