Creep resistance continuous glass fiber reinforced polyethylene prepreg tape and preparation method thereof
A glass fiber and polyethylene technology, applied in the field of material science, can solve the problems of creep resistance research of few and complete plastic substrates, and achieve the effect of improving compression resistance, improving mechanical properties and excellent mechanical properties
- Summary
- Abstract
- Description
- Claims
- Application Information
AI Technical Summary
Problems solved by technology
Method used
Examples
Embodiment 1
[0027] (1) 100 parts of low-density polyethylene; 10 parts of solid silane coupling agent; 3 parts of compatibilizer (polyethylene grafted maleic acid); antioxidant (tetra[β-(3,5-di-tert-butyl -4-hydroxyphenyl) propionate] pentaerythritol ester): 0.4 parts; tris [2.4-di-tert-butylphenyl] phosphite: 0.2 parts) a total of 0.6 parts; 40 parts of alkali-resistant glass fiber.
[0028] (2) Add low-density polyethylene, polyethylene-grafted maleic acid, solid silane coupling agent, and antioxidant in the high-speed mixer in sequence, and seal it after mixing evenly. The mixing speed is 400r / min, and the mixing time is 60s;
[0029] (3) After the mixture in step (2) is extruded, the preheated continuous glass fiber is coated. The preheating temperature of the continuous glass fiber was 120°C and the extrusion temperature of the mixture was 180°C. Cool and shape the coated continuous glass fiber strip to obtain a smooth surface and creep-resistant continuous glass fiber reinforced lo...
Embodiment 2
[0031] (1) 100 parts of linear low-density polyethylene; 20 parts of solid silane coupling agent; 5 parts of compatibilizer (polyethylene grafted maleic anhydride); antioxidant (tetra[beta-(3,5-di-tert-butyl Base-4-hydroxyphenyl) propionate] pentaerythritol ester: 0.4 parts; tris [2.4-di-tert-butylphenyl] phosphite: 0.2 parts) a total of 0.6 parts; 50 parts of alkali-resistant glass fiber.
[0032] (2) Add linear low-density polyethylene, polyethylene-grafted maleic anhydride, solid silane coupling agent, and antioxidant to the high-speed mixer in sequence, and seal it after mixing evenly. The mixing speed is 400r / min, and the mixing time is 80s;
[0033] (3) After the mixture in step (2) is extruded, the preheated continuous glass fiber is coated. The preheating temperature of the continuous glass fiber was 120°C and the extrusion temperature of the mixture was 180°C. Cool and shape the coated continuous glass fiber strip to obtain a smooth surface and creep-resistant contin...
Embodiment 3
[0035] (1) Take 100 parts of medium density polyethylene; 20 parts of solid silane coupling agent; 4 parts of compatibilizer (polyethylene grafted acrylic acid); -4-hydroxyphenyl)propionate]pentaerythritol ester: 0.6 parts; N,N'-bis-(3-(3,5-di-tert-butyl-4-hydroxyphenyl)propionyl)hexamethylenediamine: 0.3 parts) a total of 0.9 parts; 60 parts of alkali-free glass fiber.
[0036] (2) Add medium-density polyethylene, polyethylene-grafted acrylic acid, solid silane coupling agent, and antioxidant in sequence in a high-speed mixer, and seal it after mixing evenly. The mixing speed is 500r / min, and the mixing time is 60s;
[0037] (3) After the mixture in step (2) is extruded, the preheated continuous glass fiber is coated. The preheating temperature of the continuous glass fiber was 130°C and the extrusion temperature of the mixture was 180°C. The coated continuous glass fiber strip is cooled and shaped to obtain a creep-resistant continuous glass fiber reinforced medium-density...
PUM
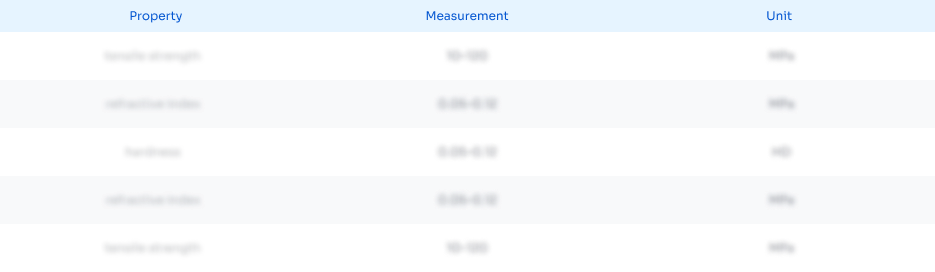
Abstract
Description
Claims
Application Information

- R&D
- Intellectual Property
- Life Sciences
- Materials
- Tech Scout
- Unparalleled Data Quality
- Higher Quality Content
- 60% Fewer Hallucinations
Browse by: Latest US Patents, China's latest patents, Technical Efficacy Thesaurus, Application Domain, Technology Topic, Popular Technical Reports.
© 2025 PatSnap. All rights reserved.Legal|Privacy policy|Modern Slavery Act Transparency Statement|Sitemap|About US| Contact US: help@patsnap.com