Bilateral double-spring driving unfolding mechanism
A deployment mechanism and dual-spring technology, which is applied to the power supply system of aerospace vehicles and other directions, can solve the problems of increasing the system weight and space requirements, increasing the risk of locking and positioning the deployment mechanism, and reducing product reliability, etc. Compact structure, reducing the impact force of deployment lock
- Summary
- Abstract
- Description
- Claims
- Application Information
AI Technical Summary
Problems solved by technology
Method used
Image
Examples
Embodiment
[0025] As attached figure 1 , Attached figure 2 And image 3 As shown, a bilateral dual-spring drive expansion mechanism includes a living hinge 1, a fixed hinge 2, a concentric shaft 3, a scroll spring 4, a lubrication pad 5, a spring stop 6, a spring outer end cover 7, and a spring inner ring Fixed sleeve 8, spring outer ring fixed shaft 9, spring outer ring fixed sleeve 10, spring outer ring fixed sleeve gland 11, lock hook 12, lock hook rotation shaft 13, lock hook positioning sleeve 14, lock hook positioning torsion spring 15, The lock hook locates the torsion spring compression rod 16, the lock hook pad 17 and the limit screw 18.
[0026] Among them, the living hinge 1 and the fixed hinge 2 are both three-dimensional quadrangular structures, and are optimized for weight reduction according to topology optimization design technology, with grooves on each surface; the middle of the fixed hinge 2 is processed with slides and slides A section of arc-shaped protrusions is symme...
PUM
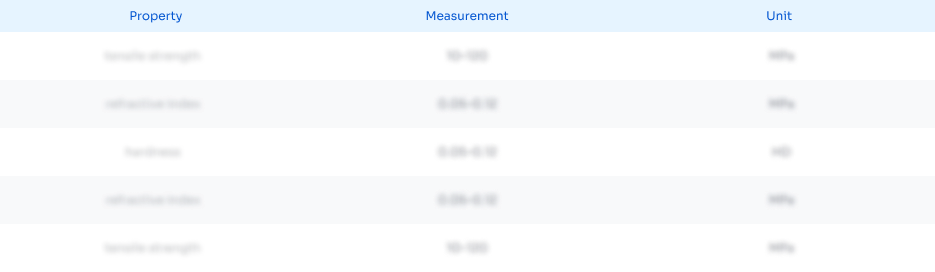
Abstract
Description
Claims
Application Information

- R&D
- Intellectual Property
- Life Sciences
- Materials
- Tech Scout
- Unparalleled Data Quality
- Higher Quality Content
- 60% Fewer Hallucinations
Browse by: Latest US Patents, China's latest patents, Technical Efficacy Thesaurus, Application Domain, Technology Topic, Popular Technical Reports.
© 2025 PatSnap. All rights reserved.Legal|Privacy policy|Modern Slavery Act Transparency Statement|Sitemap|About US| Contact US: help@patsnap.com