Ultra-wear-resistant alumina ceramic ball and preparation method thereof
A kind of alumina ceramics, super wear-resistant technology, applied in the field of super wear-resistant alumina ceramic balls and its preparation, can solve the problems of high wear of alumina ceramic balls, and achieve the effect of superior wear, high value and creative meaning
- Summary
- Abstract
- Description
- Claims
- Application Information
AI Technical Summary
Problems solved by technology
Method used
Image
Examples
Embodiment 1
[0020] Embodiment 1: alumina powder 90%, kaolin 7%, talc 0.7%, TZP 2%, rare earth (La 2 o 3 / Y 2 o 3 ) 0.3%
[0021] 1. Practicing mud
[0022] ①Put the raw material mixture and water into the ball mill according to the proportion, and run for 20 hours to release the pulp;
[0023] ② After the mud enters the tank, start the mixer and the pumping machine, filter it through the vibrating screen, and flow into the iron removal tank at the same time;
[0024] ③ After passing through the iron removal tank, the slurry is pumped to the mud press by the pump to dehydrate the slurry to make mud cake;
[0025] 2. Drying: Send the prepared mud cake into the drying room and dry at 45°C until the moisture content is 3%;
[0026] 3. Calcination synthesis: Send the dried mud cake into the kiln for calcination synthesis at 1450°C;
[0027] 4. Ball milling: put the calcined semi-finished product into a ball mill for grinding;
[0028] 5. Granulation: Send the ground slu...
Embodiment 2
[0031] Embodiment 2: alumina powder 92%, kaolin 6%, talc 0.5%, TZP 1.2%, rare earth (La 2 o 3 / Y 2 o 3 ) 0.3%
[0032] 1. Practicing mud
[0033] ①Put the raw material mixture and water into the ball mill according to the proportion, and run for 22 hours to release the pulp;
[0034] ② After the mud enters the tank, start the mixer and the pumping machine, filter it through the vibrating screen, and flow into the iron removal tank at the same time;
[0035] ③ After passing through the iron removal tank, the slurry is pumped to the mud press by the pump to dehydrate the slurry to make mud cake;
[0036] 2. Drying: Send the prepared mud cake into the drying room and dry it at 50°C until the water content is 3%;
[0037] 3. Calcination synthesis: Send the dried mud cake into the kiln for calcination synthesis at 1500 °C;
[0038] 4. Ball milling: put the calcined semi-finished product into a ball mill for grinding;
[0039] 5. Granulation: Send the ground ...
Embodiment 3
[0042] Embodiment 3: alumina powder 94%, kaolin 4%, talc 0.5%, TZP 1.4%, rare earth (La 2 o 3 / Y 2 o 3 ) 0.1 %
[0043] 1. Practicing mud
[0044] ①Put the raw material mixture and water into the ball mill according to the proportion, and run for 25 hours to release the pulp;
[0045] ② After the mud enters the tank, start the mixer and the pumping machine, filter it through the vibrating screen, and flow into the iron removal tank at the same time;
[0046] ③ After passing through the iron removal tank, the slurry is pumped to the mud press by the pump to dehydrate the slurry to make mud cake;
[0047] 2. Drying: Send the prepared mud cake into the drying room and dry it at 48°C until the moisture content is 3%;
[0048] 3. Calcination synthesis: Send the dried mud cake into the kiln for calcination synthesis at 1550 °C;
[0049] 4. Ball milling: put the calcined semi-finished product into a ball mill for grinding;
[0050] 5. Granulation: Send the gro...
PUM
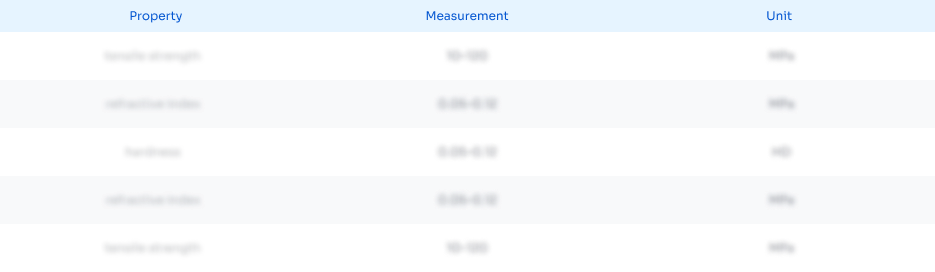
Abstract
Description
Claims
Application Information

- R&D
- Intellectual Property
- Life Sciences
- Materials
- Tech Scout
- Unparalleled Data Quality
- Higher Quality Content
- 60% Fewer Hallucinations
Browse by: Latest US Patents, China's latest patents, Technical Efficacy Thesaurus, Application Domain, Technology Topic, Popular Technical Reports.
© 2025 PatSnap. All rights reserved.Legal|Privacy policy|Modern Slavery Act Transparency Statement|Sitemap|About US| Contact US: help@patsnap.com