Method for improving cohesive strength of matrix and body of bead string
A technology of bonding strength and matrix, used in welding medium, welding equipment, tool manufacturing of sawing machine devices, etc., can solve the problem of gaps in the connection between beaded matrix and matrix, weak bonding between beaded matrix and matrix, and inability to beaded The problems of pressing ring and matrix forming, etc., can solve the problems of poor bonding, small welding deformation, and reduce tool cost.
- Summary
- Abstract
- Description
- Claims
- Application Information
AI Technical Summary
Problems solved by technology
Method used
Image
Examples
Embodiment Construction
[0024] The embodiments of the present invention will be described in detail below with reference to the accompanying drawings, but the present invention can be implemented in many different ways defined and covered by the claims.
[0025] figure 1 It is a structural schematic diagram of a method for improving the bonding strength between a beaded carcass and a substrate in a preferred embodiment of the present invention, referring to figure 1 The key to the implementation is the welding ring 3, usually the welding ring 3 is made of alloy materials such as AgCu, and the welding ring 3 is wound with a 0.8mm welding wire. When the present invention is carried out, first stand the sintered beaded carcass on the graphite backing plate 4, and keep the long end of the beaded matrix exposed upwards. At this time, it should be noted that the beaded carcass must be vertically erected and should not be inclined; secondly , put the prepared welding ring 3 on the long exposed end 2 of the...
PUM
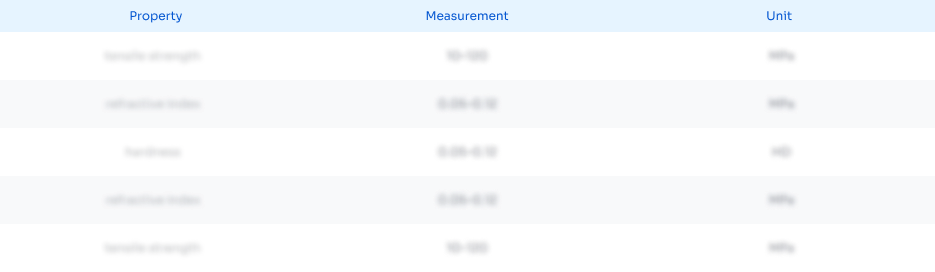
Abstract
Description
Claims
Application Information

- R&D
- Intellectual Property
- Life Sciences
- Materials
- Tech Scout
- Unparalleled Data Quality
- Higher Quality Content
- 60% Fewer Hallucinations
Browse by: Latest US Patents, China's latest patents, Technical Efficacy Thesaurus, Application Domain, Technology Topic, Popular Technical Reports.
© 2025 PatSnap. All rights reserved.Legal|Privacy policy|Modern Slavery Act Transparency Statement|Sitemap|About US| Contact US: help@patsnap.com