Porous graphene, graphene/porous metal composite material, and preparation methods of porous graphene and composite material
A technology of porous graphene and porous metal, applied in metal material coating process, coating, gaseous chemical plating, etc., can solve the problems of unadjustable pore size, complicated preparation process, low porosity, etc.
- Summary
- Abstract
- Description
- Claims
- Application Information
AI Technical Summary
Problems solved by technology
Method used
Image
Examples
preparation example Construction
[0038] In the present invention, the preparation method of the graphene / porous metal composite material is to obtain the composite material by depositing graphene on a porous metal substrate. Described method specifically comprises:
[0039] (1) Metal powder lr, Pt, Mo, W, Zn, Nb, Ta, Ru, Ti, Zr, Pd, Fe, Co, Ni, Cu, V, Rh and / or its metal oxides and other materials The powder is used as the substrate, and the porous substrate is obtained by mechanical pressing, doctor blade coating, spin coating and other methods. This scheme preferably scrape coating method. Preferably, a proper amount of binder is added to the powder and ground to form a uniform slurry. The prepared slurry is scraped on the insulating substrate to form a film by scraping, and placed in a vacuum drying oven at a certain temperature for an appropriate time.
[0040] (2) Put the dried sample into the chemical vapor deposition reaction chamber, seal and check the airtightness of the high-temperature reaction ...
Embodiment 1
[0054] Commercially available high-purity metal powders Co and CoO powder materials were mixed at a mass ratio of 1:1, 2:1, 3:1, 4:1, and 5:1 and ball milled for 0.5 hours to obtain a uniformly mixed powder. A binder with a mass fraction of 45% was added and ground into a uniform slurry. The prepared slurry was scraped on a quartz substrate to form a film by scraping, and placed in a vacuum drying oven at 70° C. for 2 hours.
[0055] Put the dried sample into the chemical vapor deposition reaction chamber, seal and check the airtightness of the high-temperature reaction chamber, discharge the residual gas in the high-temperature reaction chamber under a protective atmosphere, and then carry out temperature programming at a rate of 0.5-20°C / minute. Heat to the reaction temperature of 500°C, 600°C, 700°C, keep the temperature for 10 minutes, adjust the flow rate of hydrogen and inert gas, the gas flow rate is 50sccm, 70sccm, 90sccm and 150sccm, 200sccm, 250sccm, the reaction t...
Embodiment 2
[0058] Mix the metal powder Cu and CuO powder materials at a mass ratio of 1:1, 2:1, 3:1, 4:1, 5:1 and ball mill for 0.5 hours to obtain a uniformly mixed powder. By adding a mass fraction of 45 % binder, made into a uniform slurry by grinding. The prepared slurry was scraped on a quartz substrate to form a film by scraping, and placed in a vacuum drying oven at 70° C. for 2 hours.
[0059] Put the dried sample into the chemical vapor deposition reaction chamber, seal and check the airtightness of the high-temperature reaction chamber, discharge the residual gas in the high-temperature reaction chamber under a protective atmosphere, and then carry out temperature programming at a rate of 0.5-20°C / minute. Heat to the reaction temperature of 500°C, 600°C, 700°C, keep the temperature for 10 minutes, adjust the flow rate of hydrogen and inert gas, the gas flow rate is 50sccm, 70sccm, 90sccm and 150sccm, 200sccm, 250sccm, the reaction time is 50 minutes, 60 minutes, 70 minute. ...
PUM
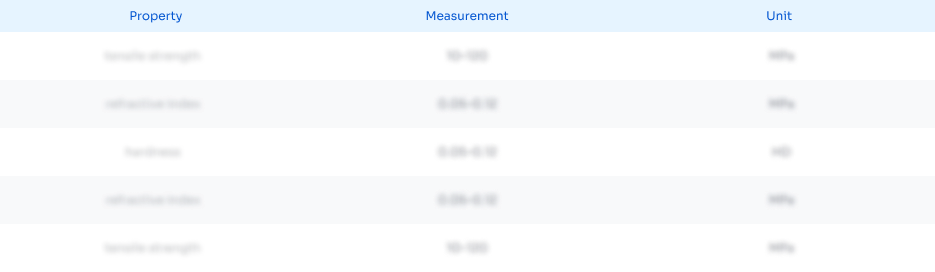
Abstract
Description
Claims
Application Information

- R&D
- Intellectual Property
- Life Sciences
- Materials
- Tech Scout
- Unparalleled Data Quality
- Higher Quality Content
- 60% Fewer Hallucinations
Browse by: Latest US Patents, China's latest patents, Technical Efficacy Thesaurus, Application Domain, Technology Topic, Popular Technical Reports.
© 2025 PatSnap. All rights reserved.Legal|Privacy policy|Modern Slavery Act Transparency Statement|Sitemap|About US| Contact US: help@patsnap.com