Method for preparing honeycomb enhanced phenolic foam composite materials
A composite material and phenolic foam technology, which is applied in the field of composite material preparation, can solve problems such as waterproof and poor flame retardancy, and achieve the effects of increasing heat insulation, simple operation process, and reducing costs
- Summary
- Abstract
- Description
- Claims
- Application Information
AI Technical Summary
Problems solved by technology
Method used
Image
Examples
Embodiment 1
[0029] A preparation method of honeycomb reinforced phenolic foam composite material, comprising the steps of:
[0030] (1) Pour the phenolic resin foaming composition into the mold 1, so that the liquid level of the phenolic resin foaming composition in the mold 1 is kept at a consistent level. Such as Figure 3-4 As shown, the mold 1 is in the shape of an open box, and has a mold cover 2 matched with the open end of the mold 1 . The opening end of the mold 1 is provided with an outward flanging 3, and the corresponding position of the flanging 3 and the mold cover 2 is provided with a pin hole 4 for connecting and fixing the mold 1 and the mold cover 2.
[0031] (2) will be as figure 2 The shown honeycomb is put into the mold 1 vertically, and placed in the phenolic resin foaming composition, so that in each honeycomb cell of the honeycomb, the amount of the phenolic resin foaming composition is the same.
[0032] Specifically, the honeycomb is an aramid paper honeycomb,...
Embodiment 2
[0037] A preparation method of honeycomb reinforced phenolic foam composite material, the difference from Example 1 is:
[0038] In step (1), the bottom surface of the mold 1 is placed on a horizontal plane, and then the phenolic resin foaming composition is poured into the mold 1, so that the level and height of the phenolic resin foaming composition in the mold 1 can be easily maintained.
[0039] In step (2), the size of the honeycomb is 2600*1300*20mm of NH-3.67-40.
Embodiment 3
[0041] A kind of preparation method of honeycomb reinforced phenolic foam composite material, the difference with embodiment 2 is:
[0042] In step (2), the size of the honeycomb is 1000*500*20mm of 4.5-45, and the honeycomb is a glass fiber honeycomb.
[0043] It should be noted that, in Examples 1-3, the phenolic resin foaming composite material is prepared from the following raw materials in parts by weight using a common method in this industry: 100 parts of phenolic resin, 0.05-1 part of emulsifier, curing agent 0.05-1 part, 5-20 parts of foaming agent. Phenolic resin, emulsifier, curing agent, and foaming agent can be selected from the corresponding raw materials commonly used in this industry. Specifically, in Examples 1-3 of the present invention, the phenolic resins, emulsifiers, curing agents, and foaming agents selected by the inventors were all purchased from Langfang Erida Thermal Insulation Building Materials Co., Ltd., and the phenolic resins were expandable ph...
PUM
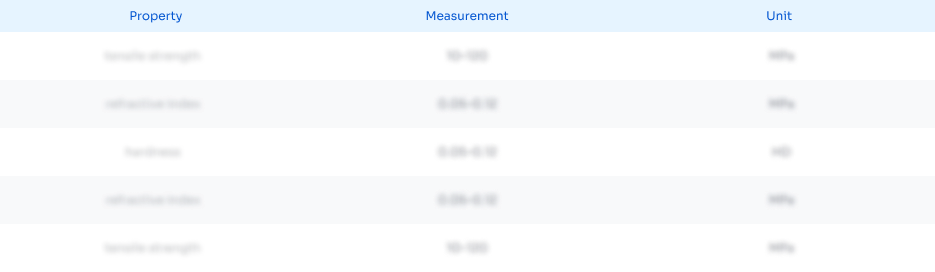
Abstract
Description
Claims
Application Information

- R&D
- Intellectual Property
- Life Sciences
- Materials
- Tech Scout
- Unparalleled Data Quality
- Higher Quality Content
- 60% Fewer Hallucinations
Browse by: Latest US Patents, China's latest patents, Technical Efficacy Thesaurus, Application Domain, Technology Topic, Popular Technical Reports.
© 2025 PatSnap. All rights reserved.Legal|Privacy policy|Modern Slavery Act Transparency Statement|Sitemap|About US| Contact US: help@patsnap.com