Age forming method and mould for aluminum lithium alloy welding structural wallboard
A welding structure, aluminum-lithium alloy technology, applied in the field of heat treatment of metal materials, can solve the problems of high strength, unsatisfactory cold forming, and difficult to meet the forming requirements of large curvature
- Summary
- Abstract
- Description
- Claims
- Application Information
AI Technical Summary
Problems solved by technology
Method used
Image
Examples
Embodiment Construction
[0020] The technical scheme of the present invention will be described in further detail below in conjunction with accompanying drawing and embodiment:
[0021] See attached Figure 1~3 As shown, the mold used for the aging forming method of the aluminum-lithium alloy welded structure wall plate includes an upper mold body 1 and a lower mold body 2, and a module 3 is arranged in the inner cavity of the lower mold body 2, and the aluminum-lithium alloy welded structure The wall plate 5 is installed above the module 3, between the upper mold body 1 and the lower mold body 2, the upper surface of the module 3 is a molding surface 4 designed according to the shape of the aluminum-lithium alloy welded structure wall plate 5, and the upper mold body 1 There are a plurality of loading bolts 6 for mechanical loading, the upper mold body 1 is installed on the lower mold body 2, the lower ends of the loading bolts 6 are pressed against the upper surface of the aluminum-lithium alloy wel...
PUM
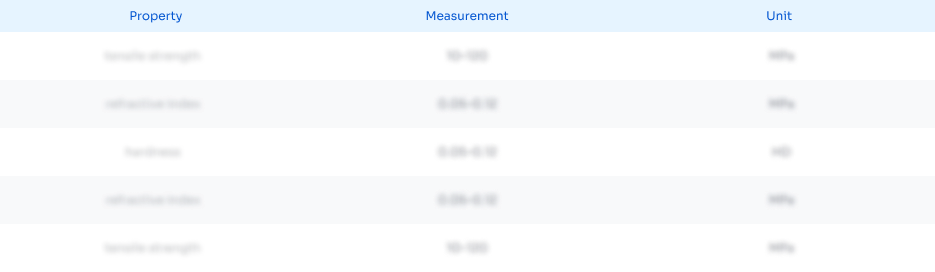
Abstract
Description
Claims
Application Information

- Generate Ideas
- Intellectual Property
- Life Sciences
- Materials
- Tech Scout
- Unparalleled Data Quality
- Higher Quality Content
- 60% Fewer Hallucinations
Browse by: Latest US Patents, China's latest patents, Technical Efficacy Thesaurus, Application Domain, Technology Topic, Popular Technical Reports.
© 2025 PatSnap. All rights reserved.Legal|Privacy policy|Modern Slavery Act Transparency Statement|Sitemap|About US| Contact US: help@patsnap.com