Metallurgical continuous casting machine roller repairing method
A repair method and continuous casting machine technology, applied in the field of metallurgical equipment repair, can solve the problems of uneven temperature distribution in the circumferential direction of the roller surface, high price, high cost, etc., and achieve the effect of increasing social employment rate and local taxation
- Summary
- Abstract
- Description
- Claims
- Application Information
AI Technical Summary
Problems solved by technology
Method used
Examples
example
[0045] The model specifications of the repaired rollers fully cover the entire continuous casting production line of the steel plant, specifically: Φ160 free roll bending section, Φ160 free roll bending section, Φ190 free roll arc section, Φ225 free roll arc section, Φ230 free roll The arc section of the roller, the straightening horizontal section of the Φ240 free roller, the straightening horizontal section of the Φ260 free roller, the straightening horizontal section of the Φ300 free roller, the straightening horizontal section of the Φ300 free roller, the arc of the driving roller in the arc section Section, and Φ220 billet thickness roller, Φ250 driving roller, Φ300 driving roller, Φ400 driving roller, their The economic benefit analysis is as follows: due to the high production price of metallurgical continuous casting products, and the maintenance cost of a single product only accounts for 1 / 4~1 / 6 of the production cost of new products, it is calculated according to the ...
PUM
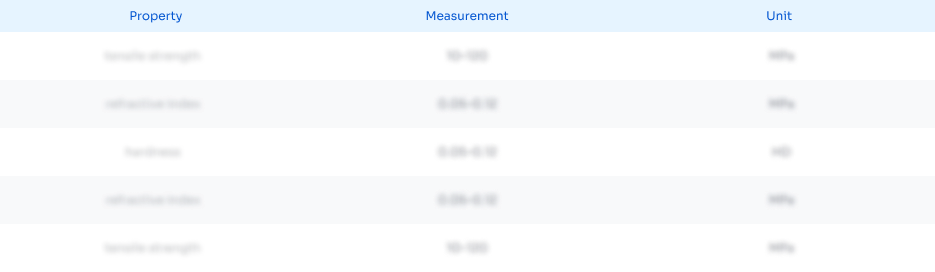
Abstract
Description
Claims
Application Information

- R&D Engineer
- R&D Manager
- IP Professional
- Industry Leading Data Capabilities
- Powerful AI technology
- Patent DNA Extraction
Browse by: Latest US Patents, China's latest patents, Technical Efficacy Thesaurus, Application Domain, Technology Topic, Popular Technical Reports.
© 2024 PatSnap. All rights reserved.Legal|Privacy policy|Modern Slavery Act Transparency Statement|Sitemap|About US| Contact US: help@patsnap.com