Preparation method of firmly-combined sandwich type purification material
A purifying material and firm combination technology, applied in chemical instruments and methods, separation methods, filtration and separation, etc., can solve the problems of low tensile strength and yield strength of electrospinning nanofibers and are not easy to filter materials, so as to improve filtration efficiency and improve filtration efficiency. The overall service life, the improvement of filtration efficiency, the effect of large specific surface area
- Summary
- Abstract
- Description
- Claims
- Application Information
AI Technical Summary
Problems solved by technology
Method used
Image
Examples
Embodiment 1
[0027] Dissolve 5.2g of PA-6 in 34.8g of formic acid, seal it and use magnetic stirring for 12 hours to fully dissolve it, and prepare 13wt% PA-6 / formic acid spinning solution for use.
[0028] Set the temperature of the melt spinning device at 150°C. After the temperature stabilizes, add 0.3g of mLLDPE raw material and heat for 30 minutes to melt the mLLDPE in the barrel. Then add 0.1g of polyethylene wax and heat for 10 minutes. Spinning is carried out under the conditions of a wire voltage of 29kV and a receiving distance of 3cm, and industrial filter cloth is used to receive fibers.
[0029] Using a self-designed electrospinning device, under the conditions of a spinning voltage of 15kV and a receiving distance of 10cm, the PA-6 / formic acid spinning solution is electrospun, and the PA-6 nanofibers are electrospun into the industry loaded with mLLDPE fibers. on the filter cloth.
[0030] The industrial filter cloth collected with mLLDPE and PA-6 nanofibers was fully dried...
PUM
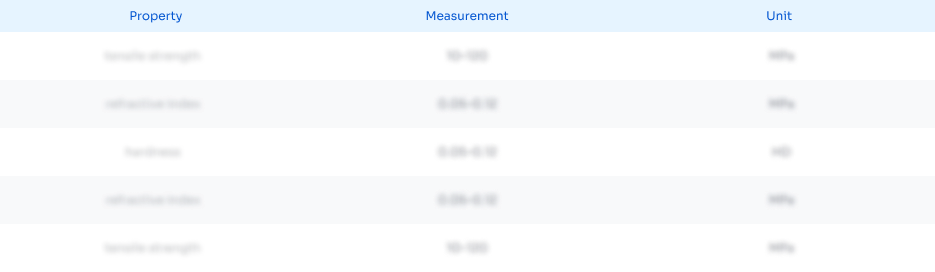
Abstract
Description
Claims
Application Information

- R&D
- Intellectual Property
- Life Sciences
- Materials
- Tech Scout
- Unparalleled Data Quality
- Higher Quality Content
- 60% Fewer Hallucinations
Browse by: Latest US Patents, China's latest patents, Technical Efficacy Thesaurus, Application Domain, Technology Topic, Popular Technical Reports.
© 2025 PatSnap. All rights reserved.Legal|Privacy policy|Modern Slavery Act Transparency Statement|Sitemap|About US| Contact US: help@patsnap.com