Copper-clad aluminum conductor production process
A production process and technology of copper-clad aluminum wire, applied in the field of copper-clad aluminum wire production process, can solve the problems of high price, drawing detachment, affecting product quality, etc., and achieve high coating bonding strength, reasonable process, and good drawing quality. Effect
- Summary
- Abstract
- Description
- Claims
- Application Information
AI Technical Summary
Problems solved by technology
Method used
Examples
Embodiment 1
[0008] A copper-clad aluminum wire production process, that is, process steps, 1. Degreasing, soaking in a chemical solvent to remove oil, 2. Cleaning, 3. Pickling, putting the aluminum wire into a pickling solution for pickling activation, 4. Pre-plating nickel, put the aluminum wire into a solution containing nickel chloride 20g / L, nickel sulfamate 100g / L, boric acid 500g / L and additives for nickel plating, 5, cleaning, 6, copper plating, the pre-nickel plating Put the aluminum wire into a solution containing 400 copper nitrate, hydroxyethylene diphosphoric acid and additives at a temperature of 30°C and a current density of 4A / dm 2 , 7, cleaning, rinse with water at a temperature of 30 ° C, 8, winding packaging.
PUM
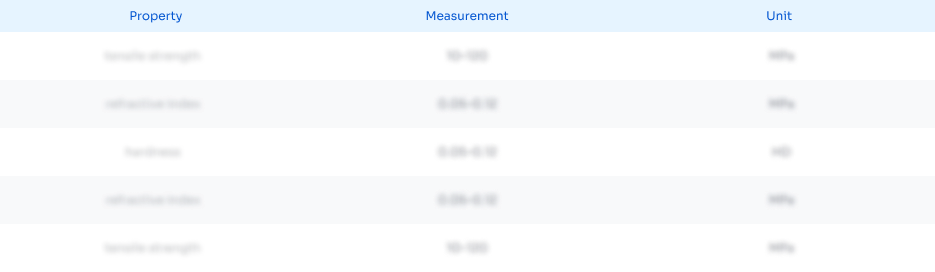
Abstract
Description
Claims
Application Information

- R&D
- Intellectual Property
- Life Sciences
- Materials
- Tech Scout
- Unparalleled Data Quality
- Higher Quality Content
- 60% Fewer Hallucinations
Browse by: Latest US Patents, China's latest patents, Technical Efficacy Thesaurus, Application Domain, Technology Topic, Popular Technical Reports.
© 2025 PatSnap. All rights reserved.Legal|Privacy policy|Modern Slavery Act Transparency Statement|Sitemap|About US| Contact US: help@patsnap.com