Heat-insulating cover structure for crystal growth furnace and production method for same
A technology of a crystal growth furnace and a production method, which is applied in the directions of crystal growth, chemical instruments and methods, post-processing devices, etc., can solve the problems of rough surface, unfavorable crystal growth, and difficult to clean, and achieves a dense and smooth inner wall surface, which is not easy to adhere to foreign matter. , the effect of reducing the impact
- Summary
- Abstract
- Description
- Claims
- Application Information
AI Technical Summary
Problems solved by technology
Method used
Image
Examples
Embodiment Construction
[0011] The present invention will be further described below in conjunction with the accompanying drawings and specific embodiments.
[0012] Such as figure 1 As shown, it is the inner wall structure of the heat preservation cover of a crystal growth furnace of the present invention. A dense ceramic thin layer 2 is sprayed on the surface of the heat preservation cover inner wall 1. The dense ceramic thin layer 2 is made of the same material as the heat preservation cover inner wall 1. . In order to prevent the sputtered ceramic thin layer 2 from being cracked due to uneven heating, the inner wall 1 of the heat preservation cover of the present invention is arranged in a grid shape, so that the ceramic thin layer 2 can be cracked naturally, so that the cracking is within a controlled range, avoiding In order to produce debris due to uneven heating and shattering. The ceramic thin layer 2 is made of the same material as the inner wall 1 of the heat preservation cover, preferab...
PUM
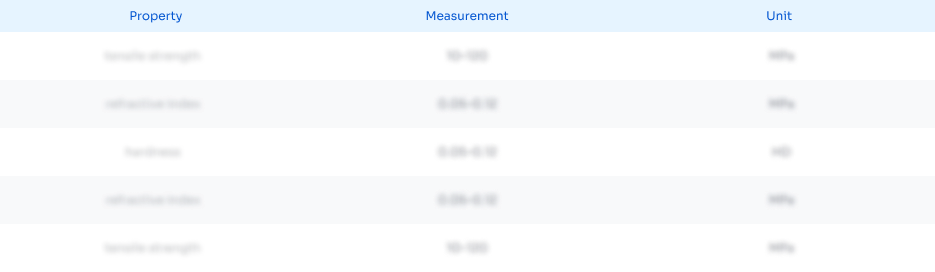
Abstract
Description
Claims
Application Information

- R&D Engineer
- R&D Manager
- IP Professional
- Industry Leading Data Capabilities
- Powerful AI technology
- Patent DNA Extraction
Browse by: Latest US Patents, China's latest patents, Technical Efficacy Thesaurus, Application Domain, Technology Topic, Popular Technical Reports.
© 2024 PatSnap. All rights reserved.Legal|Privacy policy|Modern Slavery Act Transparency Statement|Sitemap|About US| Contact US: help@patsnap.com