Solder mask printing method of thick copper plate
A printing method and thick copper plate technology, which is applied in the secondary treatment of printed circuits, coating of non-metallic protective layers, etc., can solve the problems of affecting the functionality of circuit boards, difficulty in cleaning, and reduced printing efficiency, so as to improve ink accumulation in holes Quality, Redness Improvement, Uniformity Improvement Effect
- Summary
- Abstract
- Description
- Claims
- Application Information
AI Technical Summary
Problems solved by technology
Method used
Examples
Embodiment Construction
[0023] The present invention will be further described below in conjunction with specific examples, but the specific examples do not limit the present invention in any way.
[0024] In this embodiment, solder resist printing is performed on a circuit board with a surface copper thickness of 0.28mm. The specific steps are:
[0025] Step 1. Using a traditional nylon mesh, make a screen for the copper layer area and a screen for the entire board for the area covered by the copper layer on the surface of the circuit board and the entire circuit board surface. One screen for the copper layer area is provided for the upper and lower surfaces of the circuit board, and one screen for the entire board is provided for the upper and lower surfaces of the circuit board. When making the copper layer area screen, according to the specific outer layer pattern of the circuit board, make the lower ink point corresponding to the copper layer area, the stop point corresponding to the copper-...
PUM
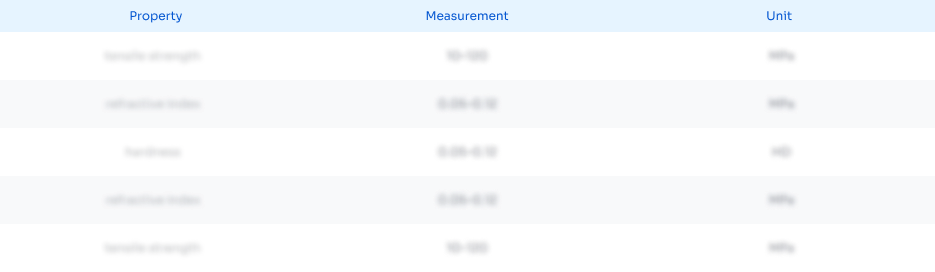
Abstract
Description
Claims
Application Information

- Generate Ideas
- Intellectual Property
- Life Sciences
- Materials
- Tech Scout
- Unparalleled Data Quality
- Higher Quality Content
- 60% Fewer Hallucinations
Browse by: Latest US Patents, China's latest patents, Technical Efficacy Thesaurus, Application Domain, Technology Topic, Popular Technical Reports.
© 2025 PatSnap. All rights reserved.Legal|Privacy policy|Modern Slavery Act Transparency Statement|Sitemap|About US| Contact US: help@patsnap.com