Method for preparing amorphous transparent zinc oxide film
A transparent zinc oxide, amorphous technology, applied in ion implantation plating, metal material coating process, coating and other directions, can solve the problems of high cost, easy to fall off, unable to carry out large-scale preparation, etc. Simple preparation process
- Summary
- Abstract
- Description
- Claims
- Application Information
AI Technical Summary
Problems solved by technology
Method used
Image
Examples
specific Embodiment 1
[0022] Specific embodiment 1, at room temperature, the magnetron reactive sputtering method was adopted, and 99.99% metal zinc was used as the cathode target in the experiment, and the anode was connected to the vacuum chamber. Install the ultrasonically cleaned substrate on the substrate fixture, and place the movable baffle between the substrate fixture and the target; close the air valves and then evacuate until the vacuum degree reaches 2×10-4Pa or more; inject an appropriate amount of argon gas; Adjust the high valve to the required working pressure; turn on the DC power supply to start sputtering for a few minutes; rotate the substrate fixture, remove the movable baffle, and start depositing the film.
[0023] The deposited metal zinc film is placed in a muffle furnace, and the temperature is raised to 400 degrees within 5 minutes in an air environment, and the film is heat-treated to obtain an amorphous transparent zinc oxide film.
specific Embodiment 2
[0024] Specific embodiment 2, at room temperature, using the magnetron reactive sputtering method, the experiment uses 99.99% metal zinc as the cathode target, and the anode is connected to the vacuum chamber. Install the ultrasonically cleaned substrate on the substrate fixture, and place the movable baffle between the substrate fixture and the target; close the air valves and then evacuate until the vacuum degree reaches 2×10-4Pa or more; inject an appropriate amount of argon gas; Adjust the high valve to the required working pressure; turn on the DC power supply to start sputtering for a few minutes; rotate the substrate fixture, remove the movable baffle, and start depositing the film.
[0025] The deposited metal zinc film is placed in a muffle furnace, and the temperature is raised to 500 degrees within 10 minutes in an air environment, and the film is heat-treated to obtain an amorphous transparent zinc oxide film.
specific Embodiment 3
[0026] Specific embodiment 3, at room temperature, the magnetron reactive sputtering method was adopted, and 99.99% metal zinc was used as the cathode target in the experiment, and the anode was connected to the vacuum chamber. Install the ultrasonically cleaned substrate on the substrate fixture, and place the movable baffle between the substrate fixture and the target; close the air valves and then evacuate until the vacuum degree reaches 2×10-4Pa or more; inject an appropriate amount of argon gas; Adjust the high valve to the required working pressure; turn on the DC power supply to start sputtering for a few minutes; rotate the substrate fixture, remove the movable baffle, and start depositing the film.
[0027] The deposited metal zinc film is placed in a muffle furnace, and the temperature is raised to 600 degrees within 20 minutes in an air environment, and the film is heat-treated to obtain an amorphous transparent zinc oxide film.
PUM
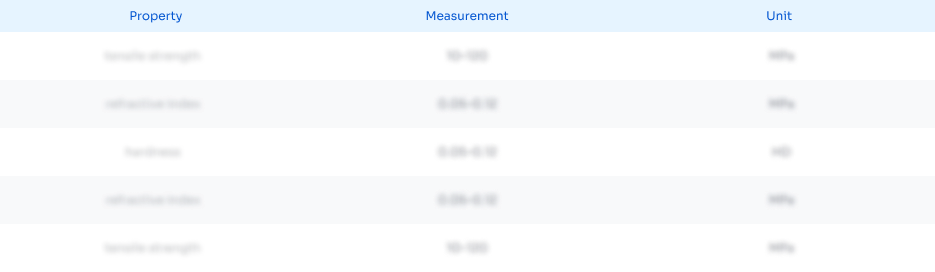
Abstract
Description
Claims
Application Information

- Generate Ideas
- Intellectual Property
- Life Sciences
- Materials
- Tech Scout
- Unparalleled Data Quality
- Higher Quality Content
- 60% Fewer Hallucinations
Browse by: Latest US Patents, China's latest patents, Technical Efficacy Thesaurus, Application Domain, Technology Topic, Popular Technical Reports.
© 2025 PatSnap. All rights reserved.Legal|Privacy policy|Modern Slavery Act Transparency Statement|Sitemap|About US| Contact US: help@patsnap.com