Hydraulic self-moving tail device
A self-moving tail and hydraulic technology, applied in the direction of conveyors, transportation and packaging, can solve the problems of injury, excessive tail traction, poor safety, etc., to achieve safe and convenient use, save manual operation, and high work efficiency Effect
- Summary
- Abstract
- Description
- Claims
- Application Information
AI Technical Summary
Problems solved by technology
Method used
Image
Examples
Embodiment Construction
[0040] like Figure 1 to Figure 3 As shown, the hydraulic self-moving tail device of the present invention includes a guide frame 18, a nose 1, a rail 2 and a tail 3 which are sequentially connected together from front to back.
[0041] combine Figure 4 to Figure 6 As shown, the left and right sides of the rear end of the guide frame 18 are respectively hinged with the front ends of the two angle-adjusting cylinders 25 through the pin shaft, and the rear ends of the two angle-adjusting cylinders 25 are respectively connected with the left and right sides of the front end of the machine head 1 through the pin shaft. Right side hinged. One end of the angle-adjusting cylinder 25 connected to the machine head 1 is higher than the other end of the angle-adjusting cylinder 25 connected on the guide frame 18 . Both angle adjustment cylinders 25 are connected with the hydraulic control system 29 through hydraulic pipelines. The hydraulic control system 29 is installed on the top o...
PUM
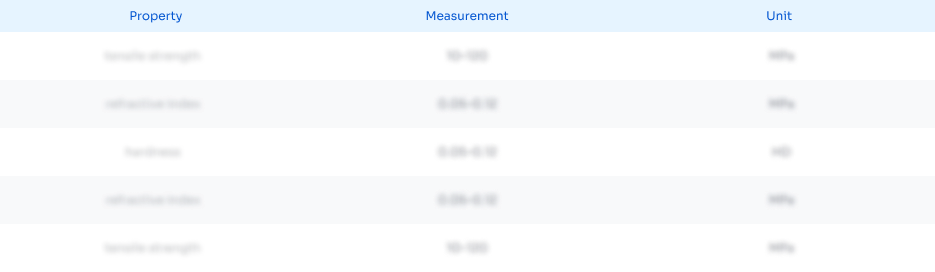
Abstract
Description
Claims
Application Information

- R&D
- Intellectual Property
- Life Sciences
- Materials
- Tech Scout
- Unparalleled Data Quality
- Higher Quality Content
- 60% Fewer Hallucinations
Browse by: Latest US Patents, China's latest patents, Technical Efficacy Thesaurus, Application Domain, Technology Topic, Popular Technical Reports.
© 2025 PatSnap. All rights reserved.Legal|Privacy policy|Modern Slavery Act Transparency Statement|Sitemap|About US| Contact US: help@patsnap.com