Joint five-degree-of-freedom docking sealing debugging equipment
A sealing and degree of freedom technology, applied in liquid tightness measurement using liquid/vacuum degree, testing of mechanical parts, testing of machine/structural parts, etc., to achieve good stability, high reliability and simple operation
- Summary
- Abstract
- Description
- Claims
- Application Information
AI Technical Summary
Problems solved by technology
Method used
Image
Examples
Embodiment Construction
[0035] The present invention includes:
[0036] 1. Bottom plate, 2. Left side plate, 3. Right side plate, 4. Top bar, 5. Bottom plate foot, 6. Lifting screw, 7. Screw nut, 8. Bottom plate copper sleeve, 9. Turbine, 10 , worm, 11, worm support seat 1, 12, worm support seat 2, 13, holding key, 14, worm holding key 2, 15, lifting handwheel, 16, positioning copper sleeve, 17, guide column, 18, fixed plate , 19. Lifting plate, 20. Bottom plate of cross table, 21. Connection block of cross table, 22. Top plate of cross table, 23. X-axis handwheel, 24. X-axis dial, 25. Y-axis handwheel, 26 , Y-axis dial, 27, indexing table handwheel, 28, indexing table dial, 29, indexing table base, 30, indexing table rotating plate, 31, sensor base plate, 32, T-shaped connection block, 33, Positioning column, 34, sensor, 35, sensor top plate, 36, connecting block, 37, lower bracket support plate, 38, lower bracket, 39, shaft cover, 40, left shaft copper sleeve, 41, left shaft seat, 42, holding Key...
PUM
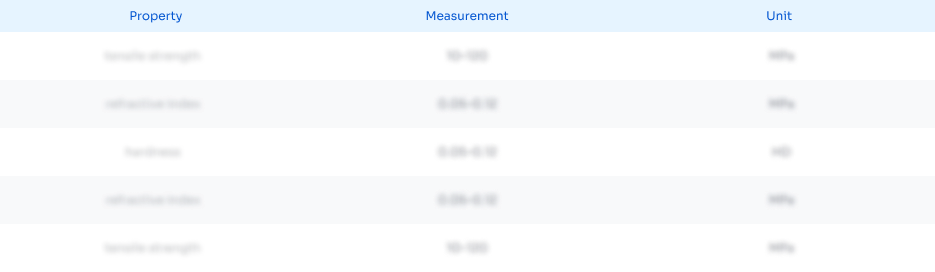
Abstract
Description
Claims
Application Information

- Generate Ideas
- Intellectual Property
- Life Sciences
- Materials
- Tech Scout
- Unparalleled Data Quality
- Higher Quality Content
- 60% Fewer Hallucinations
Browse by: Latest US Patents, China's latest patents, Technical Efficacy Thesaurus, Application Domain, Technology Topic, Popular Technical Reports.
© 2025 PatSnap. All rights reserved.Legal|Privacy policy|Modern Slavery Act Transparency Statement|Sitemap|About US| Contact US: help@patsnap.com