Manufacturing technique of highlight floor base material
A production process and floor technology, applied in the field of wood processing, to achieve the effect of high surface finish and flatness, and less cost increase
- Summary
- Abstract
- Description
- Claims
- Application Information
AI Technical Summary
Problems solved by technology
Method used
Examples
Embodiment 1
[0015] A production process for a 7.8mm E1 grade high-gloss floor substrate, comprising the steps of:
[0016] 1. Peeling: the fresh logs of poplar: pine: miscellaneous wood are 1:1:1 respectively, and the fresh logs are peeled by the peeling machine, and the peeling rate is more than 90%;
[0017] 2. Chipping: Send the peeled fresh wood to the chipper through the conveyor belt to make wood chips with a length of 15-25 mm, a width of 15-25 mm, and a thickness of 3-5 mm;
[0018] 3. Screening: For oversized (more than 25 mm) or too small (less than 3mm) pieces, they are screened;
[0019] 4. Washing: The wood chips are washed with water, on the one hand, to remove mixed sand, metal, mud and other impurities, to ensure the cleanliness of the wood chips, and on the other hand, to increase the moisture content of the wood chips appropriately;
[0020] 5. Pre-cooking and cooking: The washed wood chips are pre-steamed in a pre-cooking tank with saturated steam, and the pre-cooking ...
Embodiment 2
[0032] A production process for a 10.8mm E0 grade high-gloss floor substrate, comprising the following steps:
[0033] 1. Peeling: Fresh poplar: pine: miscellaneous wood is peeled by a peeling machine in proportion;
[0034] 2. Chipping: Send the peeled wood to the chipper through the conveyor belt to make wood chips with a length of 15-25 mm, a width of 15-25 mm, and a thickness of 3-5 mm;
[0035] 3. Screening: For oversized (greater than 25mm) or too small (less than 3mm) pieces, they are screened;
[0036] 4. Water washing: the wood chips are washed with water, on the one hand to remove mixed sand, metal, mud and other impurities to ensure the cleanliness of the wood chips, and on the other hand to appropriately increase the moisture content of the wood chips;
[0037] 5. Pre-cooking and cooking: The washed wood chips are pre-steamed in a pre-cooking tank with saturated steam, and the pre-cooking temperature is 95-100°C. The material level of the cooking tank is 2-3 mete...
PUM
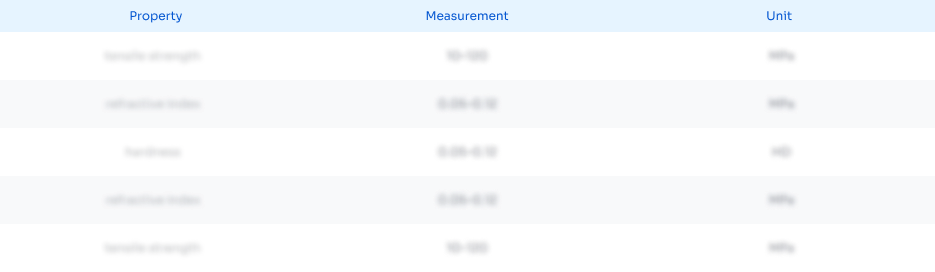
Abstract
Description
Claims
Application Information

- Generate Ideas
- Intellectual Property
- Life Sciences
- Materials
- Tech Scout
- Unparalleled Data Quality
- Higher Quality Content
- 60% Fewer Hallucinations
Browse by: Latest US Patents, China's latest patents, Technical Efficacy Thesaurus, Application Domain, Technology Topic, Popular Technical Reports.
© 2025 PatSnap. All rights reserved.Legal|Privacy policy|Modern Slavery Act Transparency Statement|Sitemap|About US| Contact US: help@patsnap.com