Automatic ink-jet blowing system for hot die forging press
A hot die forging press and inkjet technology, applied in forging/pressing/hammering machinery, forging/pressing/hammer devices, manufacturing tools, etc., can solve the problem of affecting forming quality, reducing die life, increasing energy consumption, etc. problems, to achieve the effect of shortening the production cycle, reducing labor intensity, and spraying uniform dispersion
- Summary
- Abstract
- Description
- Claims
- Application Information
AI Technical Summary
Problems solved by technology
Method used
Image
Examples
Embodiment
[0023] Example: see figure 1 , figure 2 as well as image 3 , an automatic inkjet blowing system for a hot forging press, including an inkjet system and a blowing system, both of which are installed on the upper die base 1 of a hot forging press; wherein the spray The ink system is used to simultaneously spray ink on the die chambers of the molds on the upper and lower die bases 5 of the hot forging press, and the blowing system is used to simultaneously spray the mold on the lower die base 5 of the hot forging press. The cavity is blown. The entire inkjet blowing system uses PLC control technology to control the blowing system and inkjet system; thus realizing the automation of blowing and inkjet.
[0024] The blowing system includes two air delivery pipes 21, and the two air delivery pipes 21 are installed on the lower surface of the upper mold base 1, and are located on both sides of the mold on the upper mold base 1. Described air delivery pipe 21 has an air injection...
PUM
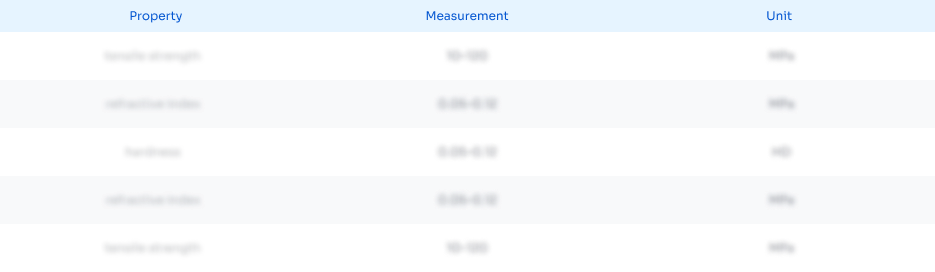
Abstract
Description
Claims
Application Information

- R&D
- Intellectual Property
- Life Sciences
- Materials
- Tech Scout
- Unparalleled Data Quality
- Higher Quality Content
- 60% Fewer Hallucinations
Browse by: Latest US Patents, China's latest patents, Technical Efficacy Thesaurus, Application Domain, Technology Topic, Popular Technical Reports.
© 2025 PatSnap. All rights reserved.Legal|Privacy policy|Modern Slavery Act Transparency Statement|Sitemap|About US| Contact US: help@patsnap.com