Wiring method for fibers for monitoring composite cylinder
A composite material and wiring method technology, applied in the direction of analyzing materials, material analysis through optical means, measuring devices, etc., can solve problems affecting test monitoring coverage, fiber failure, fiber grating failure, etc.
- Summary
- Abstract
- Description
- Claims
- Application Information
AI Technical Summary
Problems solved by technology
Method used
Image
Examples
Embodiment Construction
[0046] Below in conjunction with accompanying drawing and specific embodiment the present invention is described in further detail:
[0047] As shown in Figure 1, it is a schematic structural diagram of a composite material gas cylinder with pre-embedded optical fibers in the present invention. The composite material gas cylinder is generally a columnar structure, consisting of a gas cylinder inner liner 1 and a composite material layer 4 coated on the outer surface. The composite material gas cylinder The bottle monitoring optical fiber 2 is routed and implanted between the composite material layer 4 and the gas bottle liner 1 . The interlayer implanted gas cylinder monitoring optical fiber 2 is composed of an optical fiber sensor and a signal transmission optical fiber. Among them, the optical fiber sensor is used for measurement, and the signal transmission optical fiber is used for signal transmission. However, due to the unreasonable wiring method during the implantation...
PUM
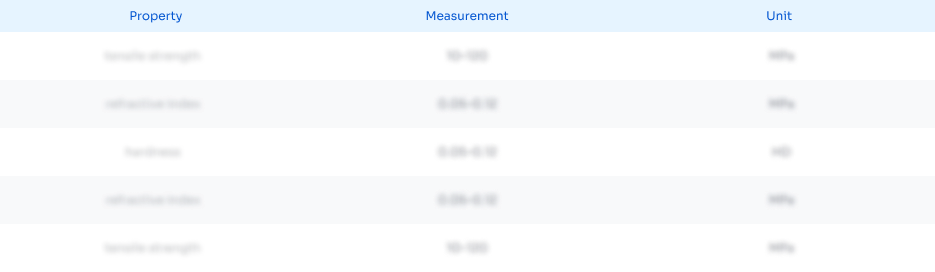
Abstract
Description
Claims
Application Information

- R&D
- Intellectual Property
- Life Sciences
- Materials
- Tech Scout
- Unparalleled Data Quality
- Higher Quality Content
- 60% Fewer Hallucinations
Browse by: Latest US Patents, China's latest patents, Technical Efficacy Thesaurus, Application Domain, Technology Topic, Popular Technical Reports.
© 2025 PatSnap. All rights reserved.Legal|Privacy policy|Modern Slavery Act Transparency Statement|Sitemap|About US| Contact US: help@patsnap.com