Method for preparing longitudinally reinforced composite preform, and composite
A composite material and prefabricated technology, applied in textiles, papermaking, non-woven fabrics, etc., can solve problems such as poor longitudinal mechanical properties, and achieve the effect of improving mechanical properties and increasing longitudinal mechanical properties.
- Summary
- Abstract
- Description
- Claims
- Application Information
AI Technical Summary
Problems solved by technology
Method used
Image
Examples
preparation example Construction
[0036] According to a typical embodiment of the present invention, a method for preparing a composite material preform is provided. The preparation method includes the following steps: a plurality of guide sleeves 10 are fixed in parallel on the guide template to form a predetermined shape; according to the cross-sectional area of the guide sleeves 10, the arrangement density of the guide sleeves, the selection of fiber bundles, and the predetermined winding path of the fibers, the fibers are determined. The position of the gap; the corresponding fiber will form the position of the gap on the guide template to set the filling sleeve 30 parallel to the guide sleeve 10; the fiber 20 is wound between a plurality of guide sleeves 10 and the filling sleeve 30; Ten fibers 20 are compacted to obtain a composite material preform. Since the filling sleeves parallel to the guide sleeves are also arranged in the gaps of the fibers, the longitudinal mechanical properties of the composit...
Embodiment
[0043] A weaving method for a hexahedron preform with a size of 100mm×100mm×50mm is listed.
[0044] 1) Select a guide sleeve 10 with a diameter of 10mm, a height of 50mm, and a carbon rod as the material, select 6k carbon fiber, and measure the cross-sectional area of the 6k fiber 20 to be 2mm; select the optimal one according to the structural shape and performance requirements of the prefabricated part The laying path, in the present embodiment, the laying path of 60°, 120°, and 180° is selected; then layered modeling is carried out along the Z direction to obtain a three-dimensional CAD model of the prefabricated part as a whole;
[0045] 2) According to the size of the guide sleeves 10, arrange 10×10 guide sleeves 10 at equal intervals on the digital guide template. Tangent; the guide sleeve 10 and the filling sleeve 30 are arranged on the guide sleeve 10 template of the geometric array layout according to the CAD model information; supported by the guide sleeve 10 and ...
PUM
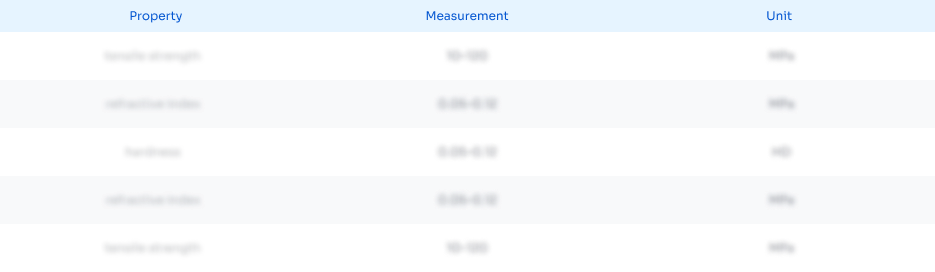
Abstract
Description
Claims
Application Information

- R&D
- Intellectual Property
- Life Sciences
- Materials
- Tech Scout
- Unparalleled Data Quality
- Higher Quality Content
- 60% Fewer Hallucinations
Browse by: Latest US Patents, China's latest patents, Technical Efficacy Thesaurus, Application Domain, Technology Topic, Popular Technical Reports.
© 2025 PatSnap. All rights reserved.Legal|Privacy policy|Modern Slavery Act Transparency Statement|Sitemap|About US| Contact US: help@patsnap.com