Laser working head with variable width of cladding layer
A technology of laser processing and cladding layer, which is applied in metal material coating process, coating and other directions, which can solve the problem that the width of the cladding layer cannot be changed in real time, and the real-time change of the width of the cladding layer cannot be realized. The laser defocus amount and the powder conveying position Real-time matching and other issues to achieve real-time changes and ensure stability
- Summary
- Abstract
- Description
- Claims
- Application Information
AI Technical Summary
Problems solved by technology
Method used
Image
Examples
Embodiment approach 1
[0038]Figure 3 shows the real-time variable working principle of the cladding layer width in the side-axis powder feeding cladding process using optical fiber transmission for the laser beam.
[0039] These include:
[0040] The optical fiber transmission group includes a transmission optical fiber 27, which is rigidly connected to the collimation unit 26 through a standard QBH interface, and the laser light 1 output by the mirror collimation unit is a near-parallel light.
[0041] The fixed reflector group includes a concave reflector 2, which is installed on the concave reflector mirror base 21 by screws, and the concave reflector mirror base 21 is installed on the concave reflector mounting body 22 by screws;
[0042] The moving reflector group, including the convex reflector 8, is installed on the convex reflector mirror seat 9 by screws, and the convex reflector mirror seat 9 is installed on the convex reflector mounting body 10 by screws;
[0043] The adjustment group i...
Embodiment approach 2
[0059] Fig. 7 is a working principle diagram of the real-time variable cladding layer width in the side-axis powder feeding cladding process where the laser beam is transmitted by the mirror group.
[0060] include:
[0061] The laser beam transmitted by the mirror group can only move the concave mirror due to the existence of the superior reflective transmission mirror, so as to implement the focal length change of the focusing system composed of convex and concave mirrors. The moving mirror groups of mode 2 and mode 1 are different, just opposite. The reflector group includes a concave reflector 2, which is mounted on the concave reflector base 21 by screws, and the convex reflector base 21 is installed on the concave reflector mounting body 22 by screws;
[0062] The fixed reflector group, including the convex reflector 8, is installed on the convex reflector mirror seat 9 by screws, and the convex reflector mirror seat 9 is installed on the convex reflector mounting body...
PUM
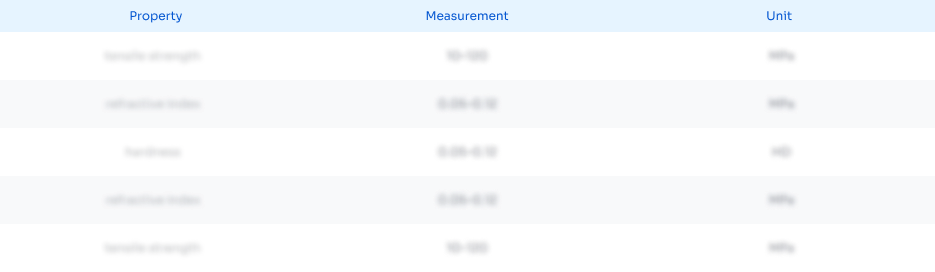
Abstract
Description
Claims
Application Information

- Generate Ideas
- Intellectual Property
- Life Sciences
- Materials
- Tech Scout
- Unparalleled Data Quality
- Higher Quality Content
- 60% Fewer Hallucinations
Browse by: Latest US Patents, China's latest patents, Technical Efficacy Thesaurus, Application Domain, Technology Topic, Popular Technical Reports.
© 2025 PatSnap. All rights reserved.Legal|Privacy policy|Modern Slavery Act Transparency Statement|Sitemap|About US| Contact US: help@patsnap.com