Thermoformable fire-proof sponge and preparation method thereof
A fireproof sponge and a production method technology, applied in the sponge field, can solve the problems of foam or sponge adhesion, insufficient tensile strength, potential safety hazards, poor flame retardancy, etc., and achieve the effects of shortening processing time, stable structure, and reducing production costs.
- Summary
- Abstract
- Description
- Claims
- Application Information
AI Technical Summary
Problems solved by technology
Method used
Image
Examples
Embodiment 1
[0064] A heat-pressable fireproof sponge, which consists of the following raw materials in parts by weight:
[0065] 5 parts by weight of PPG, 60 parts by weight of POP, 1 part by weight of TDI, 1 part by weight of MDI, 0.5 parts by weight of H 2 O, 0.3 parts by weight of SI, 0.01 parts by weight of A-1, 1.1 parts by weight of A-33, 1.1 parts by weight of catalyst, 0.5 parts by weight of white carbon black, 10 parts by weight of calcium carbonate, 8 parts by weight of open Pore agent, 5 parts by weight of fire retardant, 2 parts by weight of flame compounding agent.
[0066] The preparation method of the heat pressable fireproof sponge of the present embodiment, it is made up of the following steps:
[0067] Step (1): PPG, POP, TDI, MDI, H 2 O, SI, A-1, A-33, catalyst, white carbon black, calcium carbonate, cell opening agent, fire retardant, flame compounding agent were mixed and stirred evenly according to the weight part, and the foaming material was obtained, and the s...
Embodiment 2
[0071] A heat-pressable fireproof sponge, which is composed of the following raw materials in parts by weight: 20 parts by weight of PPG, 95 parts by weight of POP, 9 parts by weight of TDI, 3 parts by weight of MDI, 2 parts by weight of H 2 O, 0.8 parts by weight of SI, 0.05 parts by weight of A-1, 1.5 parts by weight of A-33, 1.5 parts by weight of catalyst, 5 parts by weight of white carbon, 30 parts by weight of calcium carbonate, 10 parts by weight of open Pore agent, 20 parts by weight of fire retardant, 6 parts by weight of flame compounding agent.
[0072] The preparation method of the heat pressable fireproof sponge of the present embodiment consists of the following steps:
[0073] Step (1): Put PPG, POP, TDI, MDI, H 2 O, SI, A-1, A-33, catalyst, white carbon black, calcium carbonate, cell opening agent, fireproofing agent, flame compounding agent were mixed and stirred evenly according to the weight part, and the foaming material was obtained, and the stirring sp...
Embodiment 3
[0077] A heat-pressable fireproof sponge, which is composed of the following raw materials by weight: 13 parts by weight of PPG, 78 parts by weight of POP, 5 parts by weight of TDI, 2 parts by weight of MDI, 1.2 parts by weight of H 2 O, 0.5 parts by weight of SI, 0.03 parts by weight of A-1, 1.3 parts by weight of A-33, 1.3 parts by weight of catalyst, 3 parts by weight of white carbon black, 20 parts by weight of calcium carbonate, 9 parts by weight of open Pore agent, 13 parts by weight of fire retardant, 4 parts by weight of flame compounding agent.
[0078] The preparation method of the heat pressable fireproof sponge of the present embodiment consists of the following steps:
[0079] Step (1): Put PPG, POP, TDI, MDI, H 2 O, SI, A-1, A-33, catalyst, white carbon black, calcium carbonate, cell opening agent, fire retardant, flame compounding agent were mixed and stirred evenly according to the weight part, and the foaming material was obtained, and the stirring speed wa...
PUM
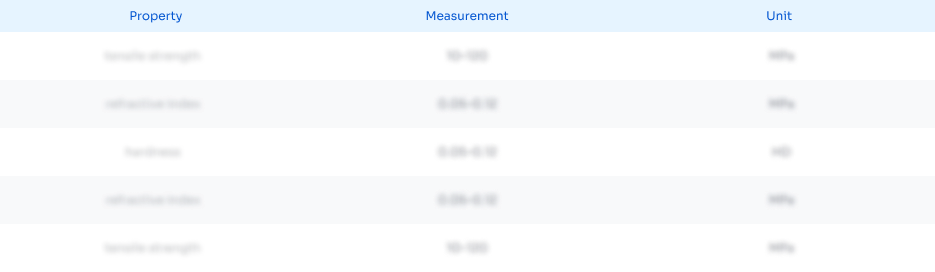
Abstract
Description
Claims
Application Information

- R&D Engineer
- R&D Manager
- IP Professional
- Industry Leading Data Capabilities
- Powerful AI technology
- Patent DNA Extraction
Browse by: Latest US Patents, China's latest patents, Technical Efficacy Thesaurus, Application Domain, Technology Topic, Popular Technical Reports.
© 2024 PatSnap. All rights reserved.Legal|Privacy policy|Modern Slavery Act Transparency Statement|Sitemap|About US| Contact US: help@patsnap.com