Equipment and technique for producing sulfur dioxide by using gypsum
A technology of sulfur dioxide and gypsum, applied in inorganic chemistry, sulfur compounds, chemical instruments and methods, etc., can solve the problems of high manufacturing cost, troublesome operation, low conversion rate, etc. easy effect
- Summary
- Abstract
- Description
- Claims
- Application Information
AI Technical Summary
Problems solved by technology
Method used
Image
Examples
Embodiment 1
[0017] refer to figure 1 The equipment for producing sulfur dioxide from gypsum in this embodiment includes a preheating extruder 1, a feeding machine 2, a calcining extruder 7, and a deaerator tank 13 with fine copper powder. The preheating extruder 1 The feed inlet of the preheating barrel 4 is connected with the outlet of the blanking machine 2, and the feed outlet is connected with the feed inlet 8 of the calcining barrel 10 of the calcining extruder 7 through the precursor discharge device 6, and the preheating The rear end of the preheating barrel 4 of the hot extruder 1 is provided with a vacuum exhaust device 5, and the rear end of the calcining barrel 10 of the calcining extruder 7 is provided with an air extraction device 12, and the air extraction device 12 The gas booster pump 11 is connected to the oxygen removal tank 13 containing fine copper powder, and the discharge port of the calcining barrel 10 of the calcining extruder 7 is provided with a discharge device ...
Embodiment 2
[0024] The equipment that utilizes gypsum to produce sulfur dioxide of the present embodiment is the same as embodiment 1.
[0025] The technique of utilizing gypsum to produce sulfur dioxide of the present embodiment comprises the following steps:
[0026] (1) Feed the gypsum powder into the preheating barrel 4 of the preheating extruder 1 through the feeder 2, remove the crystal water at 450°C, convert the crystal water into water vapor and remove it through the vacuum exhaust device 5, and Under the action of the preheating screw 3 of the preheating extruder 1, the material enters the calcining barrel 10 of the calcining extruder 7 through the precursor discharge device 6;
[0027] (2) Calcining the material in the calcining barrel 10 at 1400°C, and decomposing it into sulfur dioxide, oxygen, and calcium oxide. The sulfur dioxide and oxygen obtained enter the 600°C chamber through the air pump 12 under the action of the gas booster pump 11. The oxygen removal tank 13 for f...
PUM
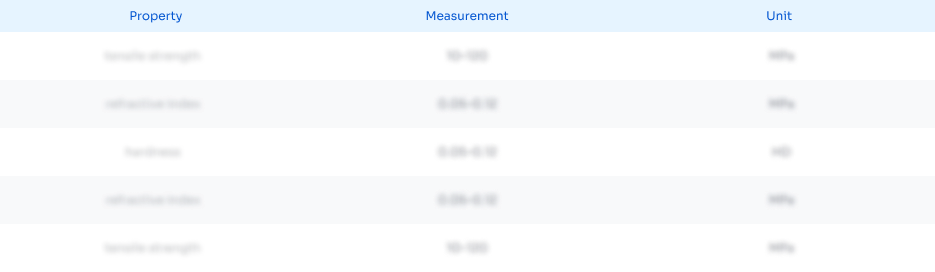
Abstract
Description
Claims
Application Information

- R&D
- Intellectual Property
- Life Sciences
- Materials
- Tech Scout
- Unparalleled Data Quality
- Higher Quality Content
- 60% Fewer Hallucinations
Browse by: Latest US Patents, China's latest patents, Technical Efficacy Thesaurus, Application Domain, Technology Topic, Popular Technical Reports.
© 2025 PatSnap. All rights reserved.Legal|Privacy policy|Modern Slavery Act Transparency Statement|Sitemap|About US| Contact US: help@patsnap.com