Comb bar for a suction nozzle for a workstation of a textile machine for creating cross-wound spools
A cross-winding bobbin and needle row technology, which is applied in the direction of thin material handling, conveying filamentous materials, transportation and packaging, etc., can solve the problems of the device not being implemented, and achieve the effect of improving looseness
- Summary
- Abstract
- Description
- Claims
- Application Information
AI Technical Summary
Problems solved by technology
Method used
Image
Examples
Embodiment Construction
[0026] figure 1 A station 2 of a textile machine for producing cross-winding bobbins, which in this exemplary embodiment is a so-called automatic cross-winding device 1 , is shown schematically in side view. Such an automatic crosswinding device 1 usually has a large number of such stations 2 of the same type arranged side by side. As known without further explanation, at these stations 2 the spinning packages 3 produced on the ring spinning machine are rewound into cross-wound packages 5 of large packages. After the cross-wound bobbin 5 has been produced, it is transferred to the cross-wound bobbin transfer device 7 arranged in the longitudinal direction of the machine by means of a (not shown) automatically working service unit (preferably a cross-wound bobbin changer) and conveyed To the bobbin loading station set on the end side of the machine, etc.
[0027] As shown in the exemplary embodiment, such an automatic crosswinder 1 usually also has a supply device in the form...
PUM
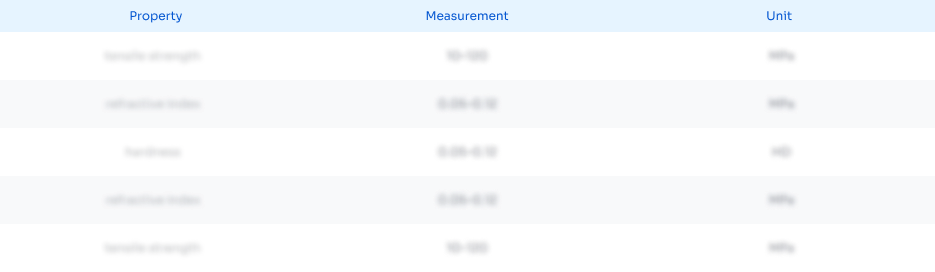
Abstract
Description
Claims
Application Information

- Generate Ideas
- Intellectual Property
- Life Sciences
- Materials
- Tech Scout
- Unparalleled Data Quality
- Higher Quality Content
- 60% Fewer Hallucinations
Browse by: Latest US Patents, China's latest patents, Technical Efficacy Thesaurus, Application Domain, Technology Topic, Popular Technical Reports.
© 2025 PatSnap. All rights reserved.Legal|Privacy policy|Modern Slavery Act Transparency Statement|Sitemap|About US| Contact US: help@patsnap.com