Spatial three-dimensional rotation parallel mechanism
A three-rotation, space technology, applied in the field of machinery, can solve the problems of large motion mass, high manufacturing cost, complex structure, etc., and achieve the effect of small motion mass, easy assembly and compact structure
- Summary
- Abstract
- Description
- Claims
- Application Information
AI Technical Summary
Problems solved by technology
Method used
Image
Examples
Embodiment Construction
[0014] The present invention will be further described in detail below in combination with specific embodiments.
[0015] Such as figure 1 As shown, a space three-rotation parallel mechanism of the present invention includes a fixed platform 1 , a moving platform 2 and a first branch 3 , a second branch 4 and a third branch 5 connecting the fixed platform 1 and the moving platform 2 .
[0016] Such as figure 2 As shown, the moving platform 2 includes a main platform 2a, a secondary platform 2b and four connecting rods 2c-2f, and the four connecting rods 2c-2f are connected by rotating pairs to form a set of planar parallelogram structures, and the four rotating pairs The axis is perpendicular to the plane where the plane parallelogram is located; the secondary platform 2b is respectively connected to a set of opposite side connecting rods 2c, 2e of the plane parallelogram through a rotary pair whose axis is perpendicular to the plane where the plane parallelogram is located,...
PUM
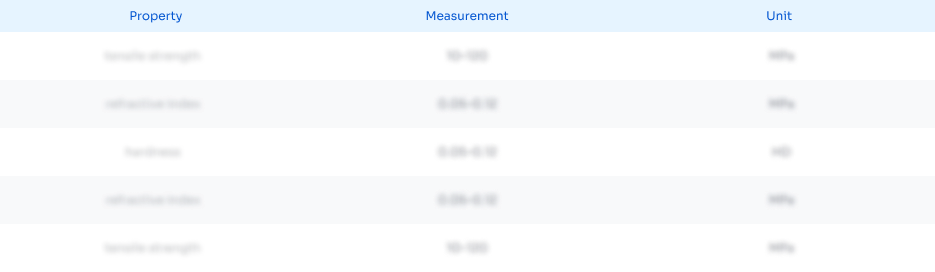
Abstract
Description
Claims
Application Information

- R&D
- Intellectual Property
- Life Sciences
- Materials
- Tech Scout
- Unparalleled Data Quality
- Higher Quality Content
- 60% Fewer Hallucinations
Browse by: Latest US Patents, China's latest patents, Technical Efficacy Thesaurus, Application Domain, Technology Topic, Popular Technical Reports.
© 2025 PatSnap. All rights reserved.Legal|Privacy policy|Modern Slavery Act Transparency Statement|Sitemap|About US| Contact US: help@patsnap.com