A rotating shaft type model hinged fixing structure and rotating shaft supporting method
A technology for fixing structures and models, applied in the field of aerospace engineering, can solve problems such as the inability to ensure that the fixed sleeve of the model does not move, the simulation that affects the flight state of the model, and the simulation of the elastic torsion that cannot be realized, so as to reduce deformation and improve The effect of supporting stiffness, relaxing torsional degrees of freedom
- Summary
- Abstract
- Description
- Claims
- Application Information
AI Technical Summary
Problems solved by technology
Method used
Image
Examples
Embodiment Construction
[0032] The present invention will be described in detail below in conjunction with the accompanying drawings and examples.
[0033] Such as figure 1 , figure 2 , image 3 As shown, a rotating shaft type model hinge fixing structure includes: a support rod 6, a rotating shaft member 11, two clips 8, and two end fixing nuts 9; the support rod 6 is radially symmetrically arranged with two Round table hole 10( Figure 4 As shown), the upper bottom of the round platform is located on the axis of the pole; the model 7 is provided with installation through holes radially, the pole 6 is located inside the model and the round platform hole on the pole is coaxial with the above-mentioned installation through hole, and the rotating shaft rod 11 is located at In the above-mentioned coaxial hole, two clips 8 with a central round hole are set on the rotating shaft rod 11 and placed in the above-mentioned round table hole and the installation through hole, and the two ends of the rotatin...
PUM
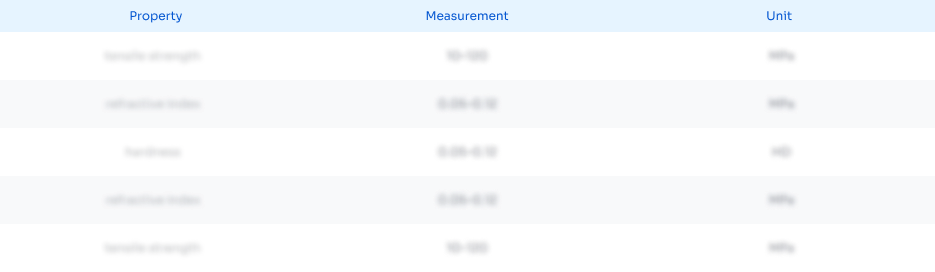
Abstract
Description
Claims
Application Information

- R&D
- Intellectual Property
- Life Sciences
- Materials
- Tech Scout
- Unparalleled Data Quality
- Higher Quality Content
- 60% Fewer Hallucinations
Browse by: Latest US Patents, China's latest patents, Technical Efficacy Thesaurus, Application Domain, Technology Topic, Popular Technical Reports.
© 2025 PatSnap. All rights reserved.Legal|Privacy policy|Modern Slavery Act Transparency Statement|Sitemap|About US| Contact US: help@patsnap.com