Integrally forming method for compound metals
A composite metal and forming method technology, applied in sports accessories, rackets, golf balls, etc., can solve the problems of material limitation, insufficient bonding strength, inconvenient production, etc., achieve convenient production, simplify the manufacturing process, improve mechanical strength and The effect of binding strength
- Summary
- Abstract
- Description
- Claims
- Application Information
AI Technical Summary
Problems solved by technology
Method used
Image
Examples
Embodiment Construction
[0023] In order to make the above-mentioned and other objects, features and advantages of the present invention more comprehensible, the preferred embodiments of the present invention are specifically cited below, together with the accompanying drawings, as follows:
[0024] Please refer to figure 2 As shown, the composite metal integral forming method of the present invention includes a preparation step S1, a forming step S2 and a sintering step S3. Wherein the preparation step S1 prepares at least two metal or alloy powders; the forming step S2 makes a composite metal blank from the at least two metal or alloy powders; the sintering step S3 sinters the composite metal blank to form a composite metal finished product.
[0025] The preparation step S1 prepares at least two metal or alloy powders, for example: at least two heterogeneous pure metal powders, at least two heterogeneous alloy powders, or at least two homogeneous but different specific gravity alloy powders. In m...
PUM
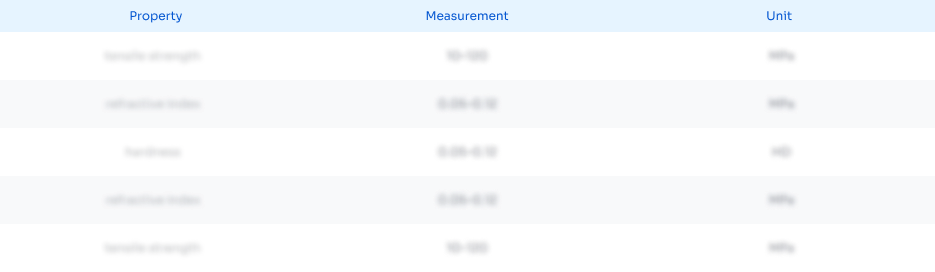
Abstract
Description
Claims
Application Information

- R&D
- Intellectual Property
- Life Sciences
- Materials
- Tech Scout
- Unparalleled Data Quality
- Higher Quality Content
- 60% Fewer Hallucinations
Browse by: Latest US Patents, China's latest patents, Technical Efficacy Thesaurus, Application Domain, Technology Topic, Popular Technical Reports.
© 2025 PatSnap. All rights reserved.Legal|Privacy policy|Modern Slavery Act Transparency Statement|Sitemap|About US| Contact US: help@patsnap.com