Low-stress and high-efficiency precise blanking method for medium-high frequency inductive heating of rod tube material
A high-frequency induction heating and precision blanking technology, applied in metal processing equipment, storage devices, feeding devices, etc., can solve the problems of low production efficiency, waste of materials, and high energy consumption
- Summary
- Abstract
- Description
- Claims
- Application Information
AI Technical Summary
Problems solved by technology
Method used
Image
Examples
Embodiment Construction
[0016] The present invention will be further described in detail below in conjunction with the accompanying drawings.
[0017] refer to figure 1 , a method for high-frequency induction heating, low-stress, high-efficiency and precise cutting of rod and tube materials, comprising the following steps:
[0018] In the first step, the rod tube material B is sent to the high-frequency induction heating device in the induction heating zone through the feeding mechanism for heating. The heating temperature range is 300-500 ° C, and the heating time is 3-10 seconds;
[0019] In the second step, after the heating is completed, the rod tube material B is sent to the unloading mechanism for unloading.
[0020] refer to figure 1 , the feeding mechanism includes an upper feeding wheel 1 and a lower feeding wheel 5, and the upper feeding wheel 1 and the lower feeding wheel 5 give a pre-tightening pressure to the rod tube material B in advance, and then rotate in the opposite direction, th...
PUM
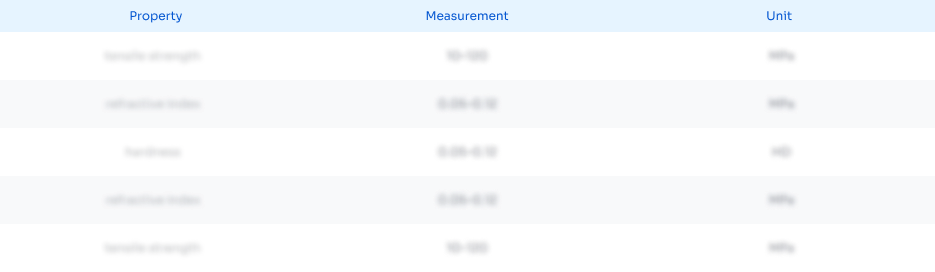
Abstract
Description
Claims
Application Information

- Generate Ideas
- Intellectual Property
- Life Sciences
- Materials
- Tech Scout
- Unparalleled Data Quality
- Higher Quality Content
- 60% Fewer Hallucinations
Browse by: Latest US Patents, China's latest patents, Technical Efficacy Thesaurus, Application Domain, Technology Topic, Popular Technical Reports.
© 2025 PatSnap. All rights reserved.Legal|Privacy policy|Modern Slavery Act Transparency Statement|Sitemap|About US| Contact US: help@patsnap.com