Flue gas cleaning system capable of switching pollutant desorption technology and adsorbent regeneration technology and method thereof
A flue gas purification system and adsorbent regeneration technology, which is applied in the field of flue gas purification, can solve the problems of inability to remove multiple pollutants synergistically, no reasonable adsorbent regeneration, and high requirements for manufacturing materials, so as to save equipment investment and operation cost, increase sulfur capacity and use efficiency, good continuity effect
- Summary
- Abstract
- Description
- Claims
- Application Information
AI Technical Summary
Problems solved by technology
Method used
Image
Examples
Embodiment 1
[0108] Such as figure 2 As shown, in this example, the flue gas purification and adsorbent regeneration system is designed for the actual flue gas volume of 200,000 to 300,000 Nm 3 / h small boiler, designed to handle flue gas volume of 300,000 Nm 3 / h, depending on the situation, two radial fixed bed reactors 1 are used in parallel for flue gas treatment, one for removal and one for regeneration. SO in general flue gas components 2 The content is 100~15000mg / Nm 3 , NO x The content is 100~2000mg / Nm 3 , It also contains some toxic heavy metal ions such as mercury and cadmium. The removal temperature is 70-150°C, and the regeneration temperature is 300-450°C; the adsorption catalyst used is columnar activated semi-coke with qualified performance and economic benefits. Through the radial fixed bed reactor 1, remove SO in the flue gas 2 , NO X , mercury, dioxin and other pollutants, and realize the joint removal of multiple pollutants in one adsorption reactor.
[0109] ...
Embodiment 2
[0113] Such as image 3 As shown, in this example, the flue gas purification and adsorbent regeneration system is designed for the actual flue gas volume of 500,000 to 700,000 Nm 3 / h of non-ferrous smelting flue gas, designed to handle flue gas volume of 600,000 Nm 3 / h, depending on the situation, three radial fixed-bed reactors 1 are used in parallel for treatment, two for removal and one for regeneration. SO in general flue gas components 2 The content is 100~15000mg / Nm 3 , NO X The content is 100~2000mg / Nm 3 , It also contains some toxic heavy metal ions such as mercury and cadmium. The removal temperature is 70-150°C, and the regeneration temperature is 300-450°C; the adsorption catalyst used is columnar activated semi-coke with qualified performance and economic benefits. Through the radial fixed bed reactor 1, remove SO in the flue gas 2 , NO X , mercury, dioxin and other pollutants, and realize the joint removal of multiple pollutants in one adsorption reactor...
Embodiment 3
[0124] When the amount of flue gas to be treated increases, more than 3 fixed bed reactors can be used in series / parallel connection by setting the flue gas valve to be purified and the flue gas valve to be purified, such as Figure 4 As shown, the flue gas purification and adsorbent regeneration system designed in this example is used in a coal-fired thermal power unit with a single unit of 600 MW in a coal-fired power plant, and the actual flue gas volume is 1 to 2 million Nm 3 / h, designed to handle flue gas volume of 1.8 million Nm 3 / h, for 8 serial / parallel radial fixed bed reactors 1 pollutant removal process / adsorbent regeneration process switching.
[0125] For the situation that the number of fixed-bed reactors 1 is more than 3, the connection relationship between the flue gas valve to be purified, the clean flue gas valve and the fixed-bed reactor 1 performs the flue gas pollutant removal process, the adsorbent regeneration process and The switching process therebe...
PUM
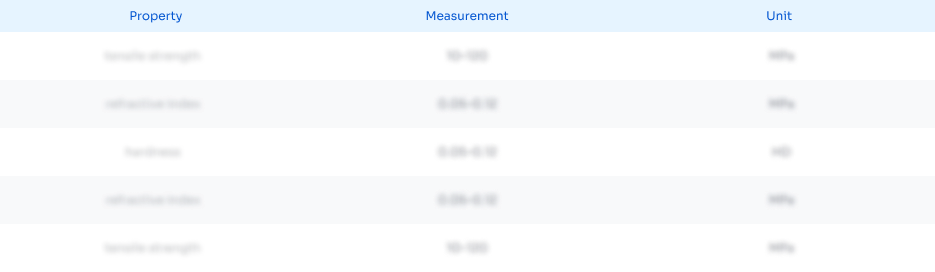
Abstract
Description
Claims
Application Information

- R&D
- Intellectual Property
- Life Sciences
- Materials
- Tech Scout
- Unparalleled Data Quality
- Higher Quality Content
- 60% Fewer Hallucinations
Browse by: Latest US Patents, China's latest patents, Technical Efficacy Thesaurus, Application Domain, Technology Topic, Popular Technical Reports.
© 2025 PatSnap. All rights reserved.Legal|Privacy policy|Modern Slavery Act Transparency Statement|Sitemap|About US| Contact US: help@patsnap.com