Method for preparing release agent for precision casting
A technology of precision casting and mold release agent, applied in casting molding equipment, molds, mold components, etc., can solve problems such as poor mold release effect, and achieve the effect of reducing scrap rate, low production cost, and improving mold release effect.
- Summary
- Abstract
- Description
- Claims
- Application Information
AI Technical Summary
Problems solved by technology
Method used
Examples
Embodiment 1
[0034] A kind of release agent for precision casting of the present embodiment, it is made of kerosene, 320 heat conduction oil, dibutyltin dilaurate, hydrogenated terphenyl, butyl acrylate, octylphenol polyoxyethylene ether, titanium dioxide, quicklime and oxidized Composed of zinc, the parts by weight of the formula are: 8 parts of kerosene, 20 parts of 320 heat transfer oil, 7 parts of dibutyltin dilaurate, 27 parts of hydrogenated terphenyl, 13 parts of butyl acrylate, octylphenol polyoxyethylene ether 8 parts, titanium dioxide 5 parts, quicklime 11 parts, zinc oxide 9 parts.
[0035] A kind of preparation method of release agent for precision casting of the present embodiment, its specific steps are as follows:
[0036] (1) Weigh 5 parts of titanium dioxide, 11 parts of quicklime, 9 parts of zinc oxide, and 8 parts of octylphenol polyoxyethylene ether according to the number of parts by mass, open the disperser, and add titanium dioxide, quicklime, and zinc oxide to the d...
Embodiment 2
[0040] A kind of release agent for precision casting of the present embodiment, it is made of kerosene, 320 heat conduction oil, dibutyltin dilaurate, hydrogenated terphenyl, butyl acrylate, octylphenol polyoxyethylene ether, titanium dioxide, quicklime and oxidized Composed of zinc, the parts by weight of the formula are: 5 parts of kerosene, 25 parts of 320 heat transfer oil, 6.5 parts of dibutyltin dilaurate, 30 parts of hydrogenated terphenyl, 10 parts of butyl acrylate, octylphenol polyoxyethylene ether 12 parts, 3 parts of titanium dioxide, 16 parts of quicklime, 7 parts of zinc oxide.
[0041] A kind of preparation method of release agent for precision casting of the present embodiment, its specific steps are as follows:
[0042] (1) Weigh 3 parts of titanium dioxide, 16 parts of quicklime, 7 parts of zinc oxide, and 12 parts of octylphenol polyoxyethylene ether in parts by mass, start the disperser, and add titanium dioxide, quicklime, and zinc oxide to the disperser i...
Embodiment 3
[0046]A kind of release agent for precision casting of the present embodiment, it is made of kerosene, 320 heat conduction oil, dibutyltin dilaurate, hydrogenated terphenyl, butyl acrylate, octylphenol polyoxyethylene ether, titanium dioxide, quicklime and oxidized Composed of zinc, the parts by weight of the formula are: 7 parts of kerosene, 23 parts of 320 heat transfer oil, 6 parts of dibutyltin dilaurate, 28 parts of hydrogenated terphenyl, 12 parts of butyl acrylate, octylphenol polyoxyethylene ether 11 parts, 4 parts of titanium dioxide, 14 parts of quicklime, 8 parts of zinc oxide.
[0047] A kind of preparation method of release agent for precision casting of the present embodiment, its specific steps are as follows:
[0048] (1) Weigh 4 parts of titanium dioxide, 14 parts of quicklime, 8 parts of zinc oxide, and 11 parts of octylphenol polyoxyethylene ether in parts by mass, start the disperser, and add titanium dioxide, quicklime, and zinc oxide to the disperser in t...
PUM
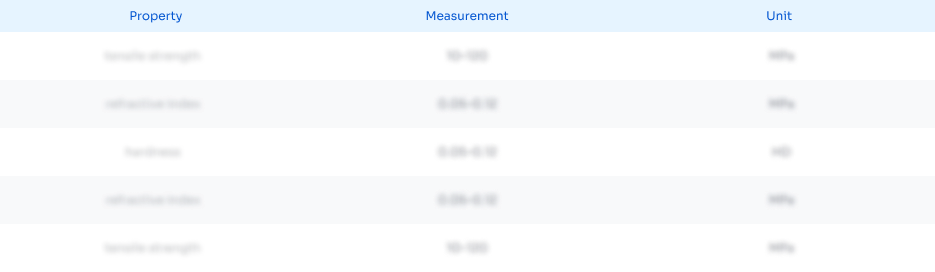
Abstract
Description
Claims
Application Information

- Generate Ideas
- Intellectual Property
- Life Sciences
- Materials
- Tech Scout
- Unparalleled Data Quality
- Higher Quality Content
- 60% Fewer Hallucinations
Browse by: Latest US Patents, China's latest patents, Technical Efficacy Thesaurus, Application Domain, Technology Topic, Popular Technical Reports.
© 2025 PatSnap. All rights reserved.Legal|Privacy policy|Modern Slavery Act Transparency Statement|Sitemap|About US| Contact US: help@patsnap.com