Composite electrical steel material
A technology of electrical steel and magnetic materials, applied in the field of alloy materials, can solve the problems of iron core magnetic properties without any contribution, affecting the energy utilization efficiency of motors, and insulating coatings without magnetic conductivity, etc., to eliminate ineffective volume and improve energy utilization. Efficiency, effect of good magnetic properties
- Summary
- Abstract
- Description
- Claims
- Application Information
AI Technical Summary
Problems solved by technology
Method used
Image
Examples
Embodiment 1
[0016] Embodiment one: figure 1 As shown, the middle layer in this embodiment is a non-oriented electrical steel base material, and the two surface layers of the electrical steel base material are composite layers of amorphous soft magnetic alloy material, forming a double-sided composite non-oriented electrical steel material.
[0017] The electrical steel base material of this embodiment adopts 50W310 grade non-oriented silicon steel base material; the amorphous soft magnetic alloy material adopts FeAlMSiB series iron-based amorphous soft magnetic alloy.
Embodiment 2
[0018] Embodiment two: figure 1 As shown, the middle layer in this embodiment is a oriented electrical steel base material, and the surface layers on both sides of the electrical steel base material are composite layers of amorphous soft magnetic alloy materials, forming a double-sided composite oriented electrical steel material.
[0019] The electrical steel base material of this embodiment adopts 27Q120 grade oriented silicon steel base material; the amorphous soft magnetic alloy material adopts FeAlMSiB series iron-based amorphous soft magnetic alloy.
Embodiment 3
[0020] Embodiment three: figure 2 As shown, the electrical steel substrate in this embodiment is non-oriented silicon steel, and the composite layer of the electrical steel substrate is an amorphous soft magnetic alloy material composite layer, forming a single-sided composite non-oriented electrical steel material.
[0021] The electrical steel base material of this embodiment adopts 50W310 grade non-oriented silicon steel base material; the amorphous soft magnetic alloy material adopts FeAlMSiB series iron-based amorphous soft magnetic alloy.
PUM
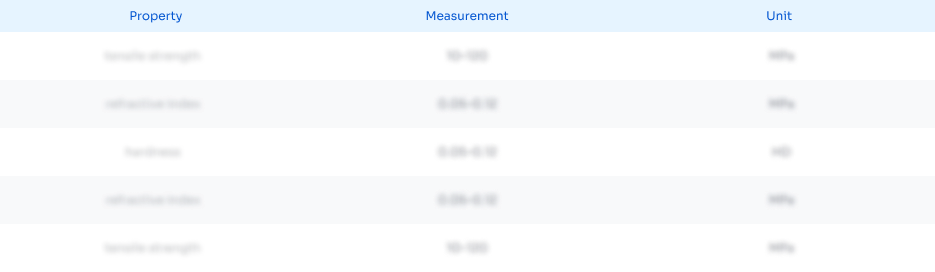
Abstract
Description
Claims
Application Information

- R&D
- Intellectual Property
- Life Sciences
- Materials
- Tech Scout
- Unparalleled Data Quality
- Higher Quality Content
- 60% Fewer Hallucinations
Browse by: Latest US Patents, China's latest patents, Technical Efficacy Thesaurus, Application Domain, Technology Topic, Popular Technical Reports.
© 2025 PatSnap. All rights reserved.Legal|Privacy policy|Modern Slavery Act Transparency Statement|Sitemap|About US| Contact US: help@patsnap.com