Hold-down mechanism for rail deburring
A compression mechanism and deburring technology, applied in the field of compression mechanism, can solve the problems of guide rail surface damage, guide rail movement, affecting deburring effect, etc., and achieve the effect of small driving force
- Summary
- Abstract
- Description
- Claims
- Application Information
AI Technical Summary
Problems solved by technology
Method used
Image
Examples
Embodiment Construction
[0015] The preferred embodiments of the present invention will be described in detail below in conjunction with the accompanying drawings, so that the advantages and features of the present invention can be more easily understood by those skilled in the art, so as to define the protection scope of the present invention more clearly.
[0016] The pressing mechanism in this embodiment is applied to a solid guide rail deburring device. as attached figure 1 to attach Figure 4 The embodiment shown is a solid guide rail deburring device, which includes a frame 1, a wire roller 5 arranged on the frame 1, a rotary drive device 7 that drives the wire roller 5 to rotate, and drives the wire roller 5 to move along the guide rail 2. The mobile driving device 6 that moves in the length direction of the tenon, the rotation axis of the wire roller 5 is perpendicular to the length direction of the guide rail 2 and perpendicular to the length direction of the tenon on the guide rail 2 ...
PUM
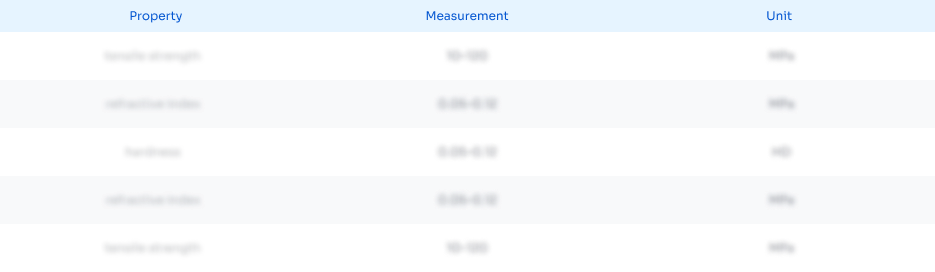
Abstract
Description
Claims
Application Information

- R&D
- Intellectual Property
- Life Sciences
- Materials
- Tech Scout
- Unparalleled Data Quality
- Higher Quality Content
- 60% Fewer Hallucinations
Browse by: Latest US Patents, China's latest patents, Technical Efficacy Thesaurus, Application Domain, Technology Topic, Popular Technical Reports.
© 2025 PatSnap. All rights reserved.Legal|Privacy policy|Modern Slavery Act Transparency Statement|Sitemap|About US| Contact US: help@patsnap.com