End-part cooling structure for rotor winding of bipolar wound rotor motor
A wire-wound motor and rotor winding technology, which is applied in the field of electric motors, can solve problems such as poor heat dissipation of the rotor, and achieve the effects of reasonable structure, ingenious design, and improved heat dissipation
- Summary
- Abstract
- Description
- Claims
- Application Information
AI Technical Summary
Problems solved by technology
Method used
Image
Examples
Embodiment Construction
[0017] The specific embodiments of the present invention will be further described below in conjunction with the accompanying drawings.
[0018] Such as figure 1 As shown, the rotor punching plate 6 is fixed on the shaft 1 through the rotor pressure rings 5 installed at the front and rear ends, and forms an integral body with the shaft 1 . The rotor pressure ring 5 at one end is fixed by the shoulder on the shaft 1 , and the rotor pressure ring 5 at the other end is positioned by the arc key 7 . The arc key 7 is placed in the groove of the shaft 1, and the arc key 7 needs to be firmly welded after being placed on the shaft 1. The rotor support 2 is heated and sleeved on the shaft 1. The rotor coils 3 are put into the slots 6 of the rotor punching sheet one by one, and the ends of the rotor coils 3 are bound with 0.3×25 epoxy mesh latitude-free tapes 4. The thickness of the latitude-free tapes 4 is calculated by the centrifugal force. Binding in sections in the axial direc...
PUM
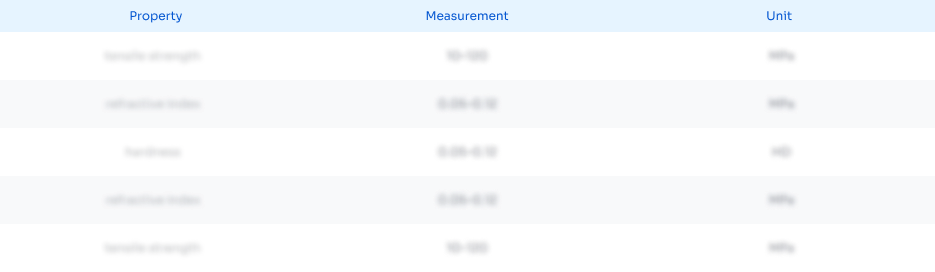
Abstract
Description
Claims
Application Information

- R&D
- Intellectual Property
- Life Sciences
- Materials
- Tech Scout
- Unparalleled Data Quality
- Higher Quality Content
- 60% Fewer Hallucinations
Browse by: Latest US Patents, China's latest patents, Technical Efficacy Thesaurus, Application Domain, Technology Topic, Popular Technical Reports.
© 2025 PatSnap. All rights reserved.Legal|Privacy policy|Modern Slavery Act Transparency Statement|Sitemap|About US| Contact US: help@patsnap.com