Beam island tower shaped piezoresistive type three-axis micro-electro-mechanical system (MEMS) high-range acceleration sensor array
An acceleration sensor and piezoresistive technology, applied in the field of MEMS sensors, can solve the problems of low mechanical precision, large volume and mass, and large coupling of acceleration sensors, and achieve the effects of reasonable structure, excessive coupling and ingenious design.
- Summary
- Abstract
- Description
- Claims
- Application Information
AI Technical Summary
Problems solved by technology
Method used
Image
Examples
Embodiment Construction
[0014] Beam island tower-shaped piezoresistive three-axis MEMS high-range acceleration sensor array, including the first six-beam double-island T-shaped structure sensor, the second six-beam double-island T-shaped structure sensor, and the four-beam cone-truncated structure sensor;
[0015] The first six-beam double-island T-shaped structure sensor includes an X-axis acceleration sensor, a Z-axis low-range acceleration sensor, and a first square silicon-based frame 1;
[0016] The X-axis acceleration sensor includes a right rectangular mass block 2, a right connecting beam 3, an upper right detection beam 4, a lower right detection beam 5, and a first Whisper composed of first-fourth pressure sensitive elements 6-9. An electrified bridge; two rectangular mass blocks on the right are suspended on the right side of the inner cavity of the first square silicon-based frame 1; The long side on the right side of 2 is fixed to the right inner wall of the first square silicon-based fr...
PUM
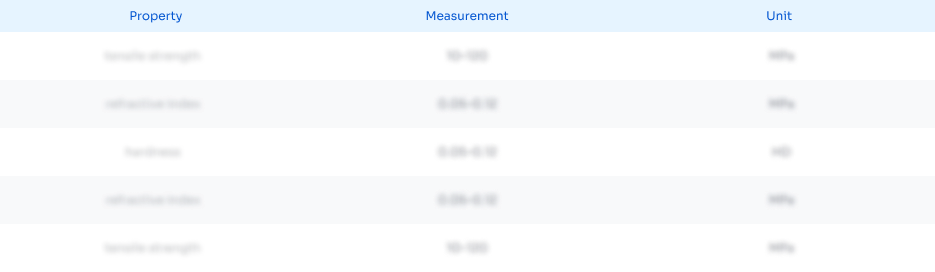
Abstract
Description
Claims
Application Information

- R&D Engineer
- R&D Manager
- IP Professional
- Industry Leading Data Capabilities
- Powerful AI technology
- Patent DNA Extraction
Browse by: Latest US Patents, China's latest patents, Technical Efficacy Thesaurus, Application Domain, Technology Topic, Popular Technical Reports.
© 2024 PatSnap. All rights reserved.Legal|Privacy policy|Modern Slavery Act Transparency Statement|Sitemap|About US| Contact US: help@patsnap.com