Automatic puncture feeding device
A feeding device and automatic technology, applied in the direction of conveyor objects, transportation and packaging, furnaces, etc., can solve the problem of putting the cloth on the special piercing frame by manual operation, and then knocking the cloth into the piercing frame with a self-made hollow hammer Then manually push the puncture frame into the oven, bake it for about 60 seconds in an environment of 200°C to 250°C, and then pull the puncture frame out of the oven and push it to the top of the mold on the hydraulic press to reduce the heat loss of the oven. and low efficiency, high labor intensity of workers, etc., to achieve the effect of simple and convenient operation, automatic control, and shortened production cycle
- Summary
- Abstract
- Description
- Claims
- Application Information
AI Technical Summary
Problems solved by technology
Method used
Image
Examples
Embodiment Construction
[0032] The present invention will be further described below in conjunction with accompanying drawing:
[0033] like figure 1 , 2 , shown in 3, a kind of automatic puncture feeding device, comprises oven 1, hydraulic press 2; Baking track 3 is set in oven 1; On the press track cylinder 5; also include automatic grabbing device 6 and double-layer frame lifting device 7; The layer frame 9 is installed on the base 8, the upper layer track 11 and the lower layer track 12 are arranged in the double layer frame 9, and the puncture frame 38 is placed on the lower layer track 11; .
[0034] like Figure 5 , 6As shown, the two ends of the base 8 are provided with gantry-type columns 23 respectively, and the optical axis guide rail 24 is installed on the column 23, and the box-type linear sliding slider 25 is arranged on the optical axis guide rail 24, and the box-type linear sliding slider 25 passes through the fixed plate 26 and Double-layer frame 9 is fixedly connected.
[003...
PUM
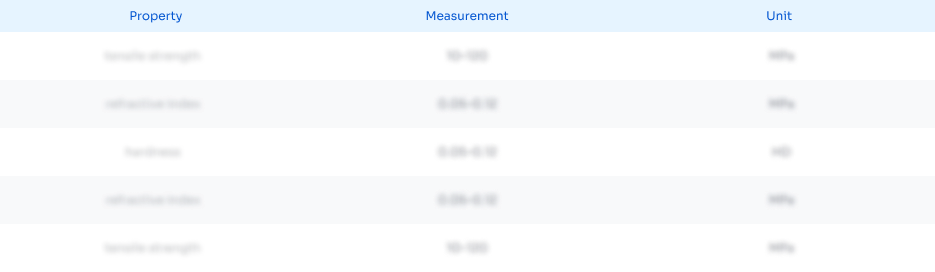
Abstract
Description
Claims
Application Information

- Generate Ideas
- Intellectual Property
- Life Sciences
- Materials
- Tech Scout
- Unparalleled Data Quality
- Higher Quality Content
- 60% Fewer Hallucinations
Browse by: Latest US Patents, China's latest patents, Technical Efficacy Thesaurus, Application Domain, Technology Topic, Popular Technical Reports.
© 2025 PatSnap. All rights reserved.Legal|Privacy policy|Modern Slavery Act Transparency Statement|Sitemap|About US| Contact US: help@patsnap.com