Continuous die processing method for processing sheet metal parts with threaded holes on the sides
A processing method and technology of sheet metal parts, applied in the direction of metal processing equipment, forming tools, manufacturing tools, etc., can solve problems such as budding hole position deviation, large automation equipment, and affecting product quality, and achieve improved accuracy, improved evaluation indicators, The effect of improving efficiency
- Summary
- Abstract
- Description
- Claims
- Application Information
AI Technical Summary
Problems solved by technology
Method used
Image
Examples
Embodiment Construction
[0028] Such as figure 1 , the back panel of the LED display is a typical metal sheet metal part with side edges, with folded edges on all four sides (always referred to as side edge 1 in this patent), and there are many hooks on the bottom surface and side edge 1, Process details such as long-distance undulations, positioning holes, protrusions, engraved explanatory text, chamfering, etc., including the threaded hole 2 related to the present invention. Moreover, these process details require high precision, and there must be no deviation, otherwise it will affect the assembly and service life of the display.
[0029] The invention includes a processing device, especially a structure for realizing tapping in a continuous die.
[0030] Such as figure 2 , image 3 Structural embodiment of the above structure: a vertically downward lead screw 4 is fixed on the upper die 3 through a fixing device, and a tap fixing device 6 is fixed on the lower die 5. The connection relationshi...
PUM
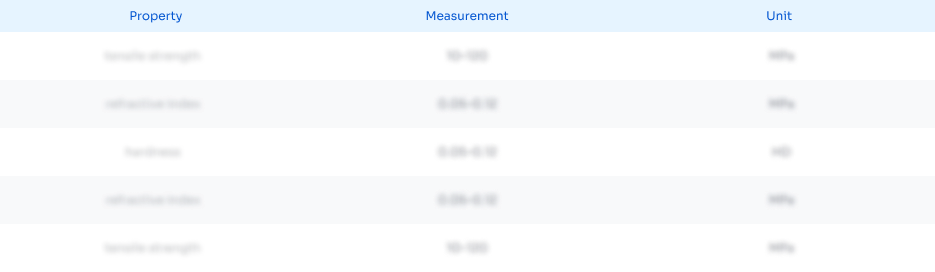
Abstract
Description
Claims
Application Information

- Generate Ideas
- Intellectual Property
- Life Sciences
- Materials
- Tech Scout
- Unparalleled Data Quality
- Higher Quality Content
- 60% Fewer Hallucinations
Browse by: Latest US Patents, China's latest patents, Technical Efficacy Thesaurus, Application Domain, Technology Topic, Popular Technical Reports.
© 2025 PatSnap. All rights reserved.Legal|Privacy policy|Modern Slavery Act Transparency Statement|Sitemap|About US| Contact US: help@patsnap.com