Method for manufacturing amorphous oxidation film aluminum foil
A production method and oxide film technology, applied in the directions of aluminum oxide/aluminum hydroxide, capacitor parts, capacitor electrodes, etc., can solve the problems of large internal resistance, capacitor failure, and excessive change rate, and achieve the effect of small loss
- Summary
- Abstract
- Description
- Claims
- Application Information
AI Technical Summary
Problems solved by technology
Method used
Image
Examples
Embodiment Construction
[0014] Below in conjunction with embodiment the present invention is further described.
[0015] A method for making an amorphous oxide film aluminum foil, comprising the steps of:
[0016] A. Choose medium and high pressure corroded aluminum foil, the thickness of medium and high pressure corroded aluminum foil is 75um ~ 120um, and the corroded foil with a corroded aperture of 0.05 microns or more;
[0017] B. Perform a low-temperature chemical conversion process to form amorphous crystalline Al 2 o 3 into foil.
[0018] The low-temperature chemical formation process includes: ①Oxalic acid treatment: the temperature of the oxalic acid solution is 10°C to 30°C, and the solubility of oxalic acid is between 1% and 10%; ②At least three stages of chemical formation are carried out, and ammonium pentaborate or boric acid is used in the chemical formation process Technology, the chemical formation solution in the chemical formation process adopts ammonium pentaborate or boric aci...
PUM
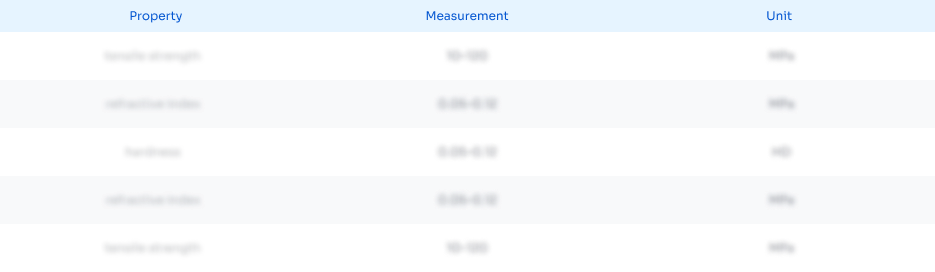
Abstract
Description
Claims
Application Information

- R&D
- Intellectual Property
- Life Sciences
- Materials
- Tech Scout
- Unparalleled Data Quality
- Higher Quality Content
- 60% Fewer Hallucinations
Browse by: Latest US Patents, China's latest patents, Technical Efficacy Thesaurus, Application Domain, Technology Topic, Popular Technical Reports.
© 2025 PatSnap. All rights reserved.Legal|Privacy policy|Modern Slavery Act Transparency Statement|Sitemap|About US| Contact US: help@patsnap.com